Nachdem ich schon in der Weihnachtszeit die Blattfedern für meine 10,25"-Ns1 konstruiert und berechnet hatte, konnte ich jetzt meine erste Semesterferienwoche nutzen, um mich als Federnschmied zu versuchen.
Ein 1:1-Modell aus Pappe habe ich zur Sicherheit mal probeweise eingebaut.
Federmodell_eingebaut (maschinist)
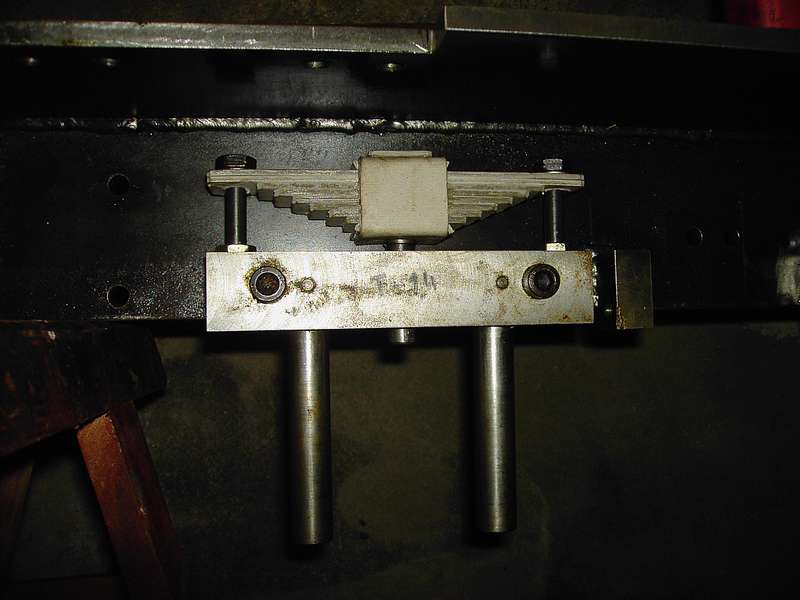
Für die 4 Blattfedern mit je 8 Lagen wurden benötigt: 4 m Federstahl 30x3 mm der Güte Ck 75 (ungehärtet), 50 cm Flachstahl 40x5 mm (Federbunde) und 30 cm Flachmaterial 20x3 mm für Keile.
Federstahl (maschinist)
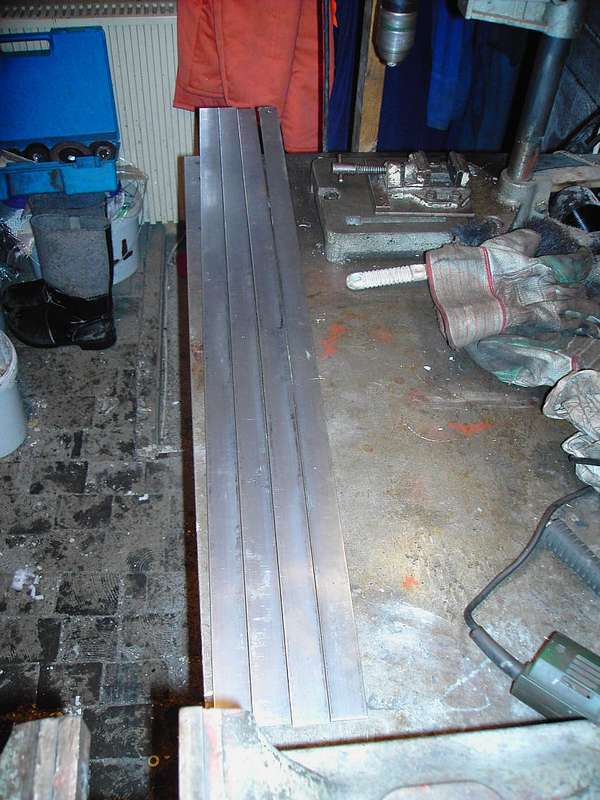
Der Federstahl wurde zunächst mittels Trennschleifer (1,5 mm Trennscheibe ermöglichst genauen sauberen Schnitt) auf die entsprechenden Längen gekürzt.
Federbl_tter_abgel_ngt (maschinist)
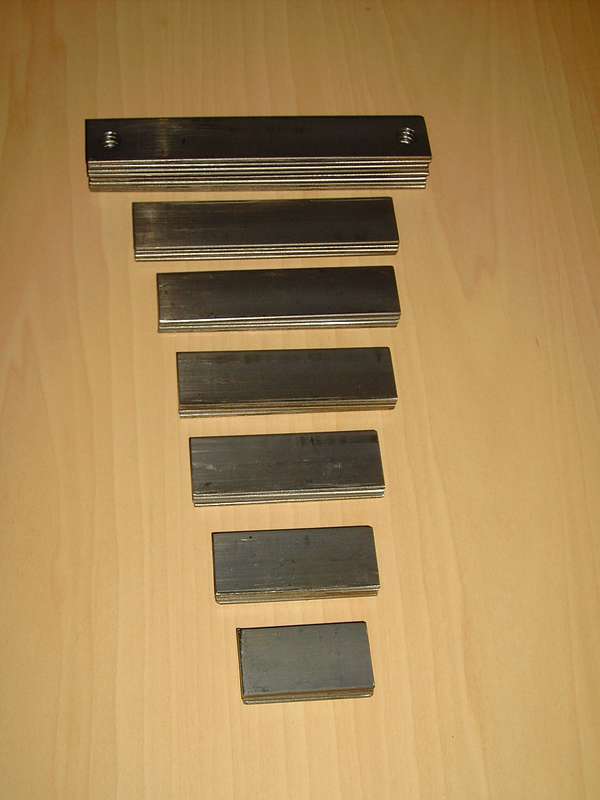
Jede Feder erhält 2 Hauptfederblätter in deren Enden Langlöcher 10x12 mm für die Federspannschrauben eingebracht wurden.
Damit die einzelnen Federlagen später nicht verrutschen können, erhalten sie in Blattmitte eine warzenförmige Vertiefung. Damit die Lagen ohne Spalt aufeinanderliegen können, müssen Innen- und Außenradius der Warze übereinstimmen.
Schnitt_durch_Federblatt (maschinist)
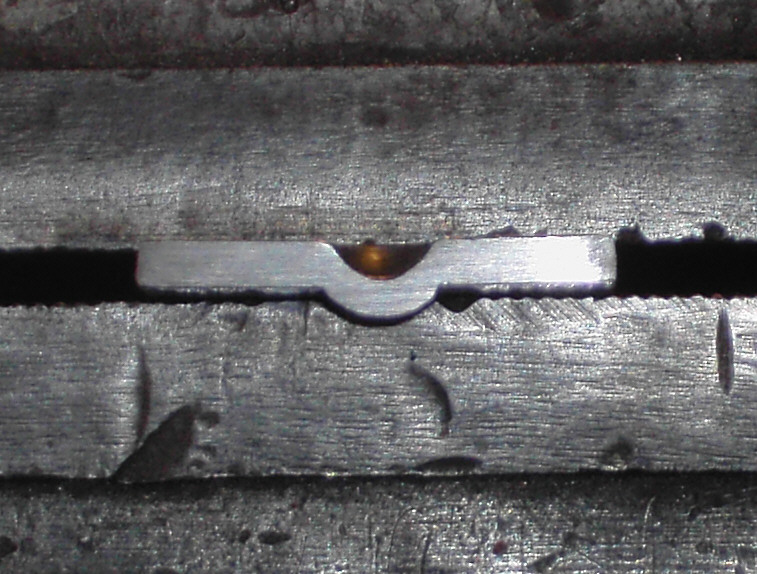
Die Herstellung der Warze erfolgt in einem eigens dafür angefertigten Preßgesenk. 2 Niederhalterschrauben verhindern eine Verwerfung des Federblattes, die mittige Positionierung erfolgt über einen verstellbaren Spindelanschlag.
Warzenpre_gesenk01 (maschinist)
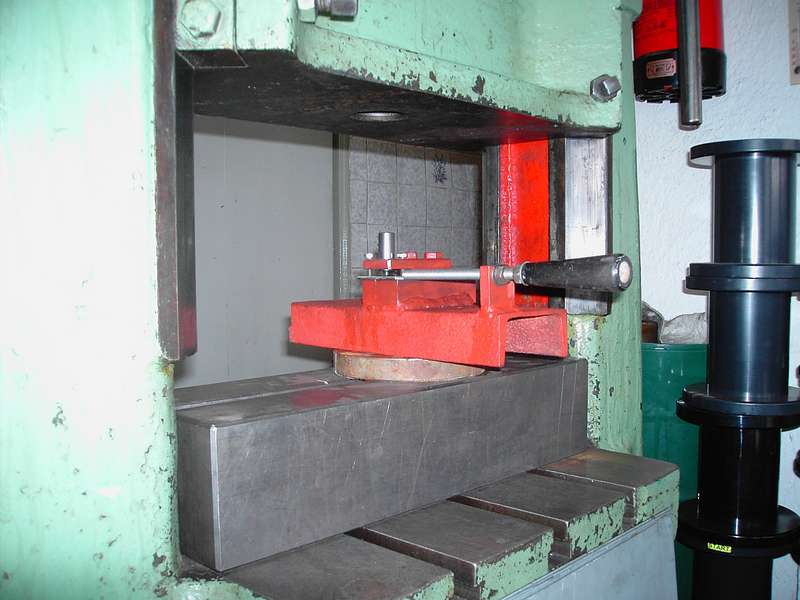
In eine mittlere Handspindelpresse eingebaut, drückt der gehärteter Preßstempel das umzuformende Material in die halbkugelförmige Vertiefung (mit rundgeschliffenem Spiralbohrer gefertigt)des Gesenkblockes. Hierbei ist auf gute Schmierung zu achten, um Material und Gesenk zu schonen und eine gute Operflächenqualität zu erreichen.
Warzenpre_gesenk02 (maschinist)
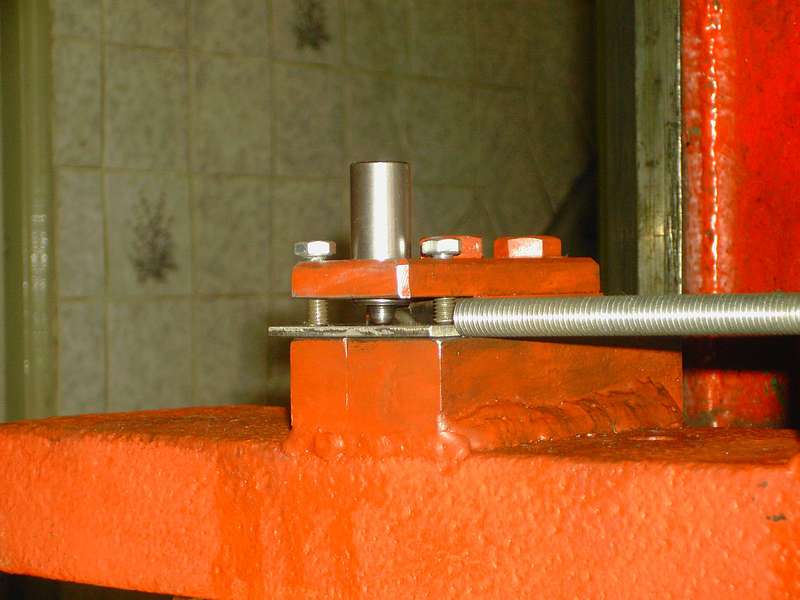
In einer knappen Stunde wurden auf diese Weise die 32 Federblätter gepreßt.
Federbl_tter_gepre_t (maschinist)
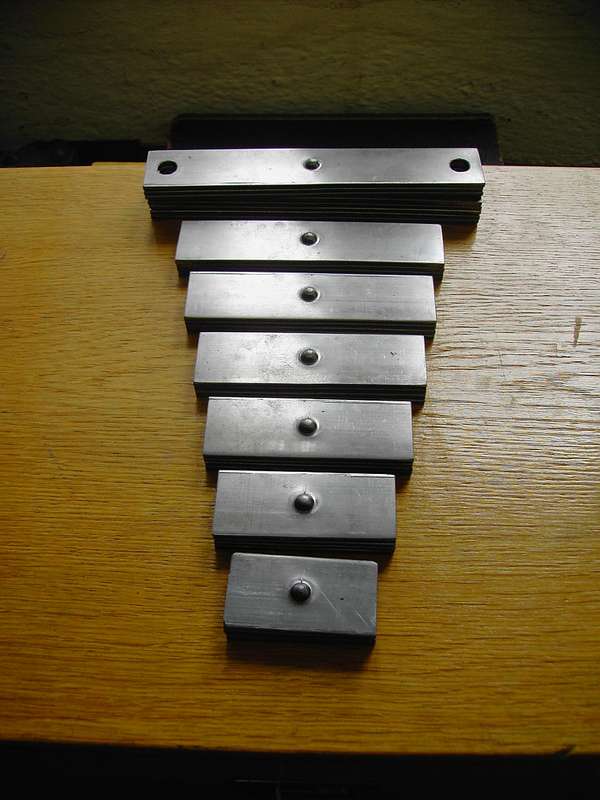
Da die Federn bei einer Ns 1 vergleichsweise hart sind, kann auf eine Vorsprengung der Lagen verzichtet werden. Wichtig ist jedoch ein gewisses Spiel der Federspannschraubenschäfte in der Feder, welches durch das Auffräsen der Bohrungen in den Hauptfederblättern zu Langlöchern gewährleistet wird.
Die Federblätter wurden im Anschluß bei ca. 830°C in Öl gehärtet und bei ca. 350°C angelassen.
Federbl_tter_geh_rtet_und_angelassen (maschinist)
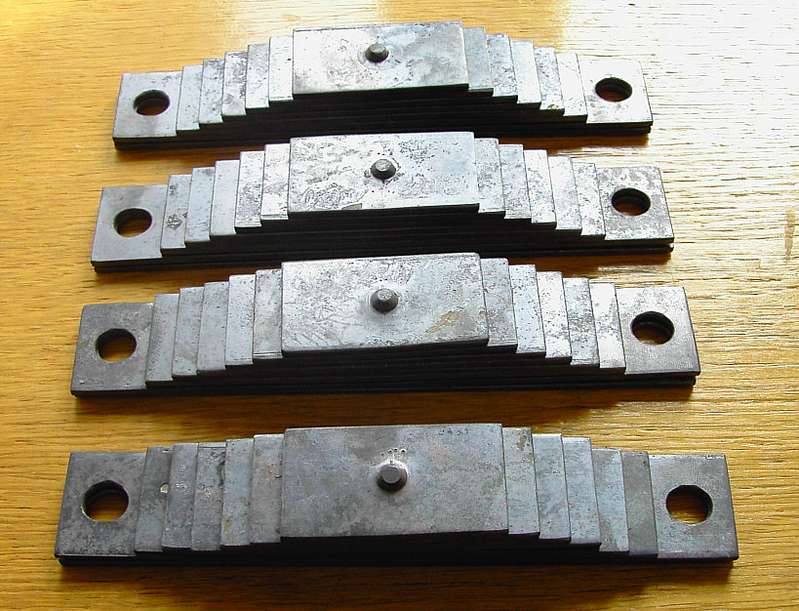
Die Federbunde wurden aus Flachmaterial 40x5 mm geschmiedet. Um ein gutes Anliegen des Bundes an den Federlagen zu ermöglichen ist die Einhaltung enger Toleranzen von großer Bedeutung. Hierfür erfolgte das Schmieden in mehreren Schritten um einem 4-Kantdorn 30x30 mm.
Zunächst wird der auf etwa 900°C erwärmte Flachstab zwecks bessere Handhabung im ganzen zwischen Dorn und Schraubstock eingespannt und durch eine schweren Handhammer mit wenigen kräftigen Schlägen abgekantet.
Federbund_biegen_01 (maschinist)
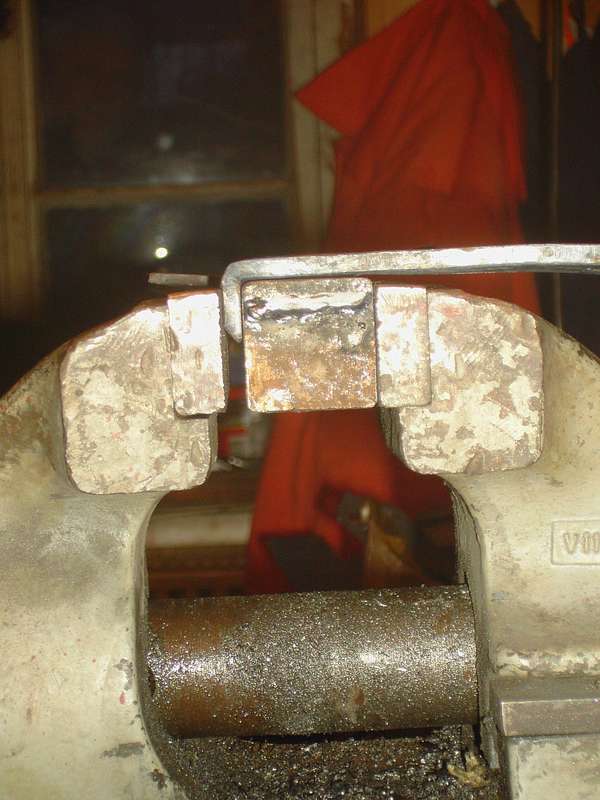
Federbund_biegen_02 (maschinist)
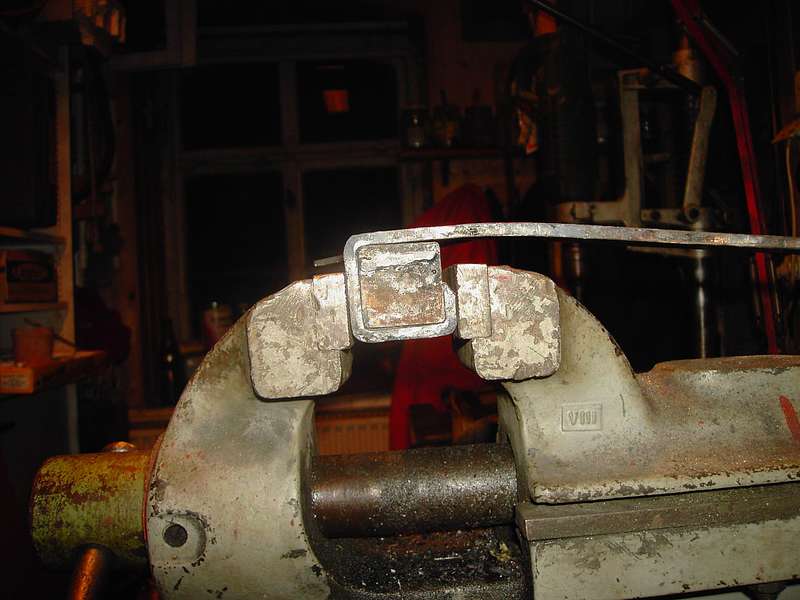
Vor dem letzten Abkanten wird der Stab auf die erforderliche Länge gekürzt und auch für das spätere Schweißen angefast.
Federbund_biegen_03 (maschinist)
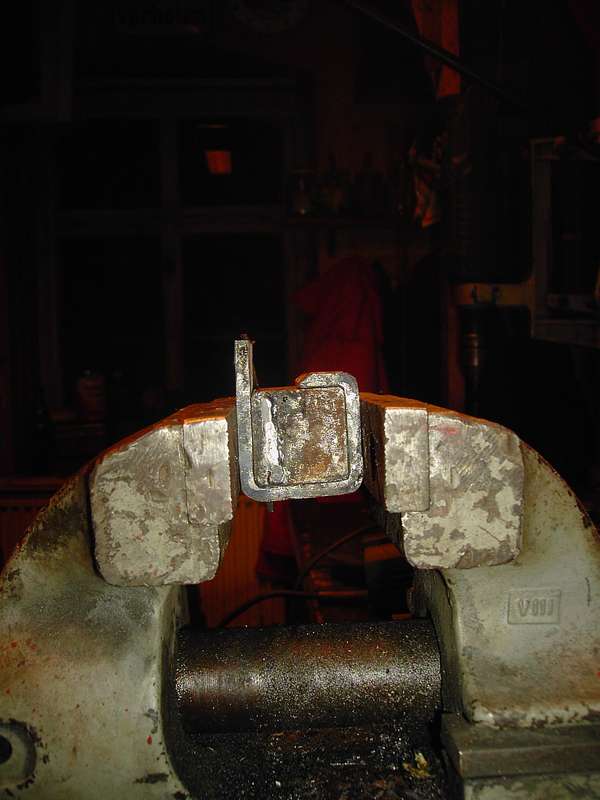
Federbund_biegen_04 (maschinist)
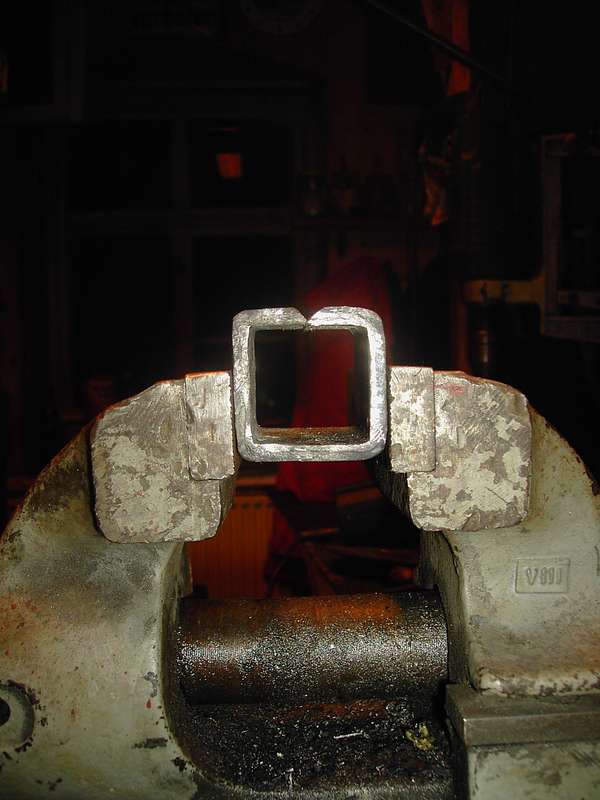
Nach dem Entfernen von Schmutz und Zunder erfogt das Schweißen des Stumpfstoßes mit einer V-Naht.
Federbund_schwei_en (maschinist)
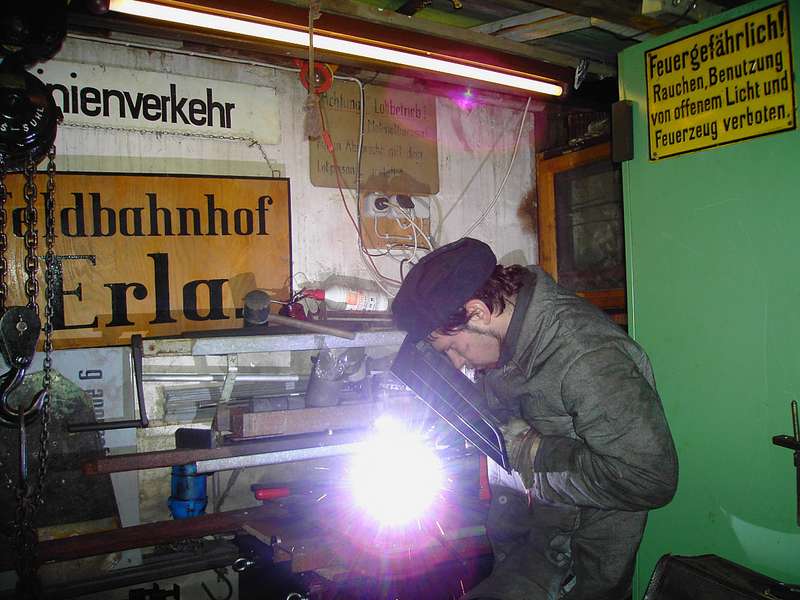
Die Naht wird im Anschluß verschliffen um das parallele Aufschweißen einer Verstärkung zu ermöglichen. Diese ermöglicht später das Fertigen einer Gewindebohrung mit ausreichender Länge für eine Druckschraube, welche die Federlagen im Bund zusammenspreßt.
Die durch die, beim Schweißen eingebrachte Wärme, verursachten thermischen Spannungen können bei dynamisch beanspruchten Bauteilen wie dem Federbund im Material zu Rissen führen und sollten daher durch Glühen (ca. 800°C, ohne Abschrecken)aufgebaut werden.
Federbund_gl_hen (maschinist)
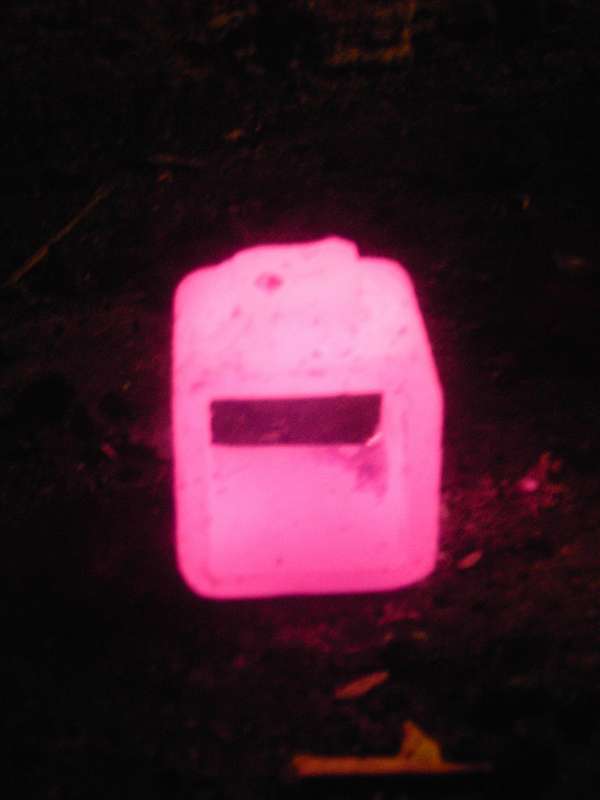
Nach dem Reinigen des abgekühlten Federbundes konnte es an den Zusammenbau gehen. Unter das Federpaket wurde noch eine Beilage eingelegt, die wegen der Eckenradien des Bundes etwas schmaler gehalten ist. Der Bund wird durch Hammerschläge, unter Zuhilfenahme eines Hartholzklotzes, über das Federpaket getrieben und zentriert. Durch eine Druckschraube erfogt das Zusammenpressen der Lagen, bis kein Luftspalt mehr vorhanden ist. Diese wird danach herausgeschraubt und zwischen oberem Hauptfederblatt und Federbund ein Flachkeil (mit Bohrung für Schraube) eingeschlagen.
Die Druckschraube wird zum Schluß wieder eingeschraubt und mittels Kontermutter gegen Herausdrehen gesichert.
Blattfeder_zusammengebaut01 (maschinist)
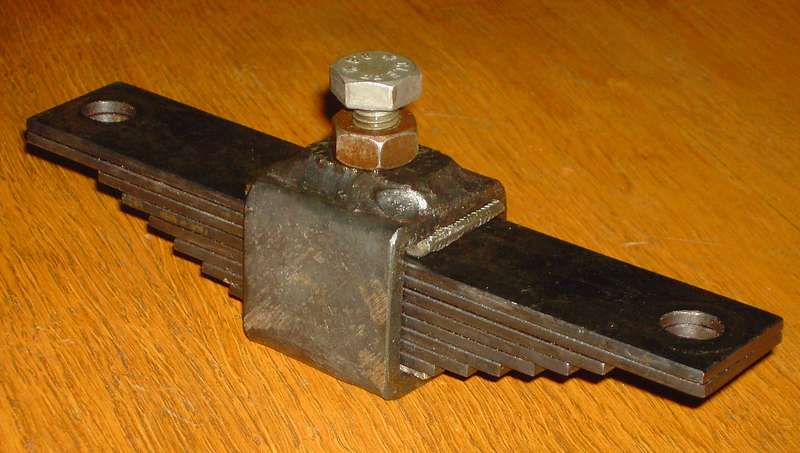
Blattfeder_zusammengebaut (maschinist)

Blattfeder_eingebaut (maschinist)
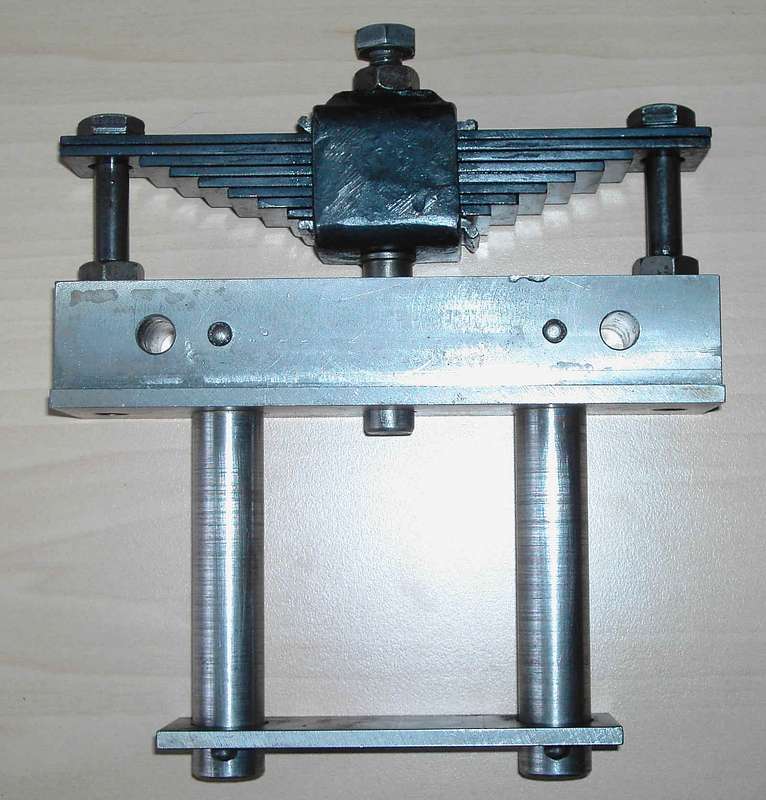
Als Korrosionsschutz ist eine Tauchbehandlung mit Elaskon vorgesehen, daß aber erst noch beschafft werden muß.
Soweit bis heute, inzwischen bin ich über den Achswellen, das ist angenehmer als die Schmiederei, die mir noch jetzt in den Knochen sitzt...

Mit gefederten Grüßen Sven