Re: Serpollet-Dampftriebwagen.
Verfasst: So 8. Mär 2009, 10:23
Hallo,
wie versprochen geht die Nachrüstung der Dampftriebwagens weiter, wenn auch nur in kleinen Schritten.
Bild35 (dampfsachse)
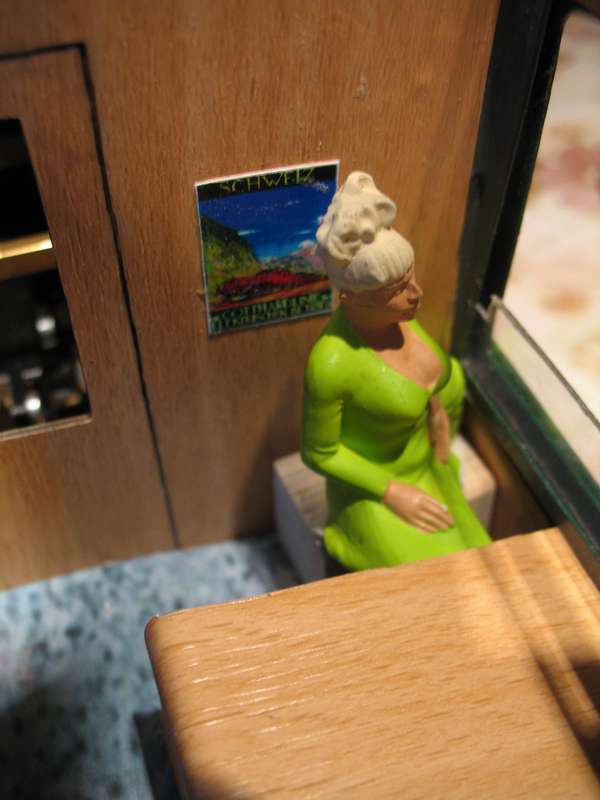
Reklame
Zunächst wurden an den Stirnseiten der Abteile die in Reisezugwagen üblichen Reklametafeln angebracht. Dazu habe ich solche Reklame der Jahre 1900 bis 1920 ausgewählt, einer Zeit also, als die Werbung noch nicht "erfunden" war. Einer Zeit aber, welche der Betriebszeit des Triebwagens entsprach. Ausreichende Vorlagen wurden mir dazu freunlicherweise von rs-modelle zur Verfügung gestellt. Diese habe ich auf maßstabsgerechte Größe kopiert und mit Holzkaltleim auf die Abteilwände geklebt. Anschließend habe ich das ganze mit farblosen Mattlack übersprüht.
Wie ihr dem Bild entnehmen könnt, sitzen meine Fahrgäste derzeit noch auf eher kistenähnlichen Holzklötzen. Selbstverständlich war das nur eine vorrüber gehende Verlegenheitslösung.
Bild36 (dampfsachse)
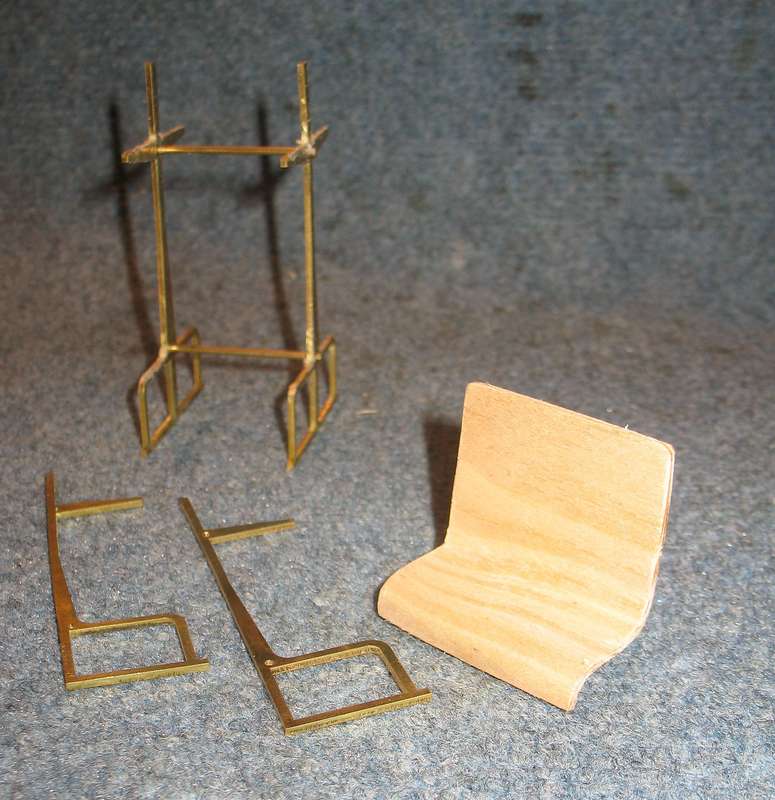
Sitzbankbau
Das obige Bild läßt schon die angestrebte Lösung erahnen. Die aus 1,5 mm Messingblech bestehenden Seitenteile habe ich durch 2 x 0,3 mm Ms-Rohre miteinander verbunden. Dazu dienen mir M 1,6 mm Messingschrauben.
Der Sitzschalenbau aus Echtholz gestaltete sich schwieriger als anfangs angenommen. Echtholzfurnier wurde über einen Wasserdampfbad ausreichend erhitzt und gewässert um anschließend in einer Form ohne Wärmezuführung langsam zu trocknen. Aus der Form entnommen, war diese Schale für jede Weiterbearbeitung zu instabil. Das sehr dünne, getrocknete Holzfurnier riß in der Holzmaserung schon beim "bloßen ansehen". Veränderung der Radien und ein Variieren der Trockenzeiten ergaben kein befriedigendes Ergebnis.
Nun habe ich zwei fertig geformte Sitzschalen vorsichtig mit Holzkaltleim über einander laminiert. Dazu konnte ich zum trocknen wieder die Form von der Sitzbankausformung verwenden. Das war die Lösung. Die Schale erreichte nicht nur durch ihre doppelte Materialstärke, sondern besonders durch die augehärtete Leimschicht ihre ausreichende Festigkeit. Da ich für die paar Sitzschalen nur eine Form angefertigt habe und eine Großstückzahl nicht herzustellen gedenke, wird der Weiterbau im wesentlichen von den Trockenzeiten bestimmt. Will sagen, die Fortsetzung des Bauberichtes wird etwas auf sich warten lassen und ich komme gut über den Rest des Winters.
Bis dahin nette Grüße vom
dampfsachsen
Gerhard
wie versprochen geht die Nachrüstung der Dampftriebwagens weiter, wenn auch nur in kleinen Schritten.
Bild35 (dampfsachse)
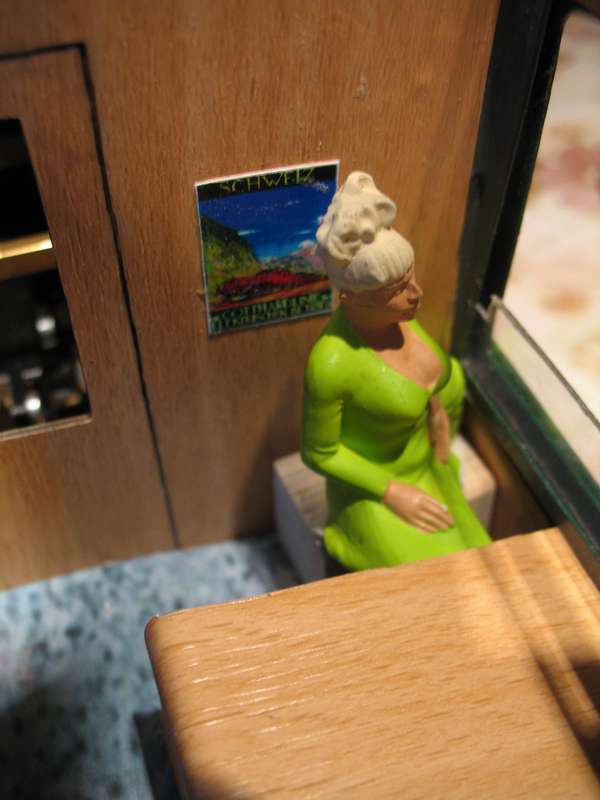
Reklame
Zunächst wurden an den Stirnseiten der Abteile die in Reisezugwagen üblichen Reklametafeln angebracht. Dazu habe ich solche Reklame der Jahre 1900 bis 1920 ausgewählt, einer Zeit also, als die Werbung noch nicht "erfunden" war. Einer Zeit aber, welche der Betriebszeit des Triebwagens entsprach. Ausreichende Vorlagen wurden mir dazu freunlicherweise von rs-modelle zur Verfügung gestellt. Diese habe ich auf maßstabsgerechte Größe kopiert und mit Holzkaltleim auf die Abteilwände geklebt. Anschließend habe ich das ganze mit farblosen Mattlack übersprüht.
Wie ihr dem Bild entnehmen könnt, sitzen meine Fahrgäste derzeit noch auf eher kistenähnlichen Holzklötzen. Selbstverständlich war das nur eine vorrüber gehende Verlegenheitslösung.
Bild36 (dampfsachse)
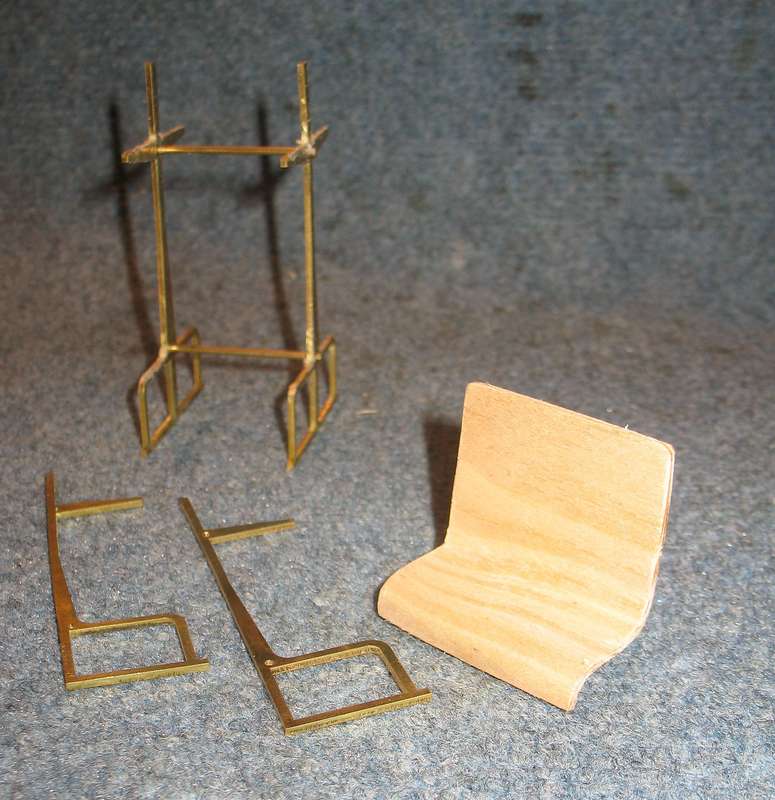
Sitzbankbau
Das obige Bild läßt schon die angestrebte Lösung erahnen. Die aus 1,5 mm Messingblech bestehenden Seitenteile habe ich durch 2 x 0,3 mm Ms-Rohre miteinander verbunden. Dazu dienen mir M 1,6 mm Messingschrauben.
Der Sitzschalenbau aus Echtholz gestaltete sich schwieriger als anfangs angenommen. Echtholzfurnier wurde über einen Wasserdampfbad ausreichend erhitzt und gewässert um anschließend in einer Form ohne Wärmezuführung langsam zu trocknen. Aus der Form entnommen, war diese Schale für jede Weiterbearbeitung zu instabil. Das sehr dünne, getrocknete Holzfurnier riß in der Holzmaserung schon beim "bloßen ansehen". Veränderung der Radien und ein Variieren der Trockenzeiten ergaben kein befriedigendes Ergebnis.
Nun habe ich zwei fertig geformte Sitzschalen vorsichtig mit Holzkaltleim über einander laminiert. Dazu konnte ich zum trocknen wieder die Form von der Sitzbankausformung verwenden. Das war die Lösung. Die Schale erreichte nicht nur durch ihre doppelte Materialstärke, sondern besonders durch die augehärtete Leimschicht ihre ausreichende Festigkeit. Da ich für die paar Sitzschalen nur eine Form angefertigt habe und eine Großstückzahl nicht herzustellen gedenke, wird der Weiterbau im wesentlichen von den Trockenzeiten bestimmt. Will sagen, die Fortsetzung des Bauberichtes wird etwas auf sich warten lassen und ich komme gut über den Rest des Winters.
Bis dahin nette Grüße vom
dampfsachsen
Gerhard