das Dach ist fertig.
Ich konnte meinen Wunsch das es abnehmbar ist umsetzen.
20201115_175358 (Steffel)
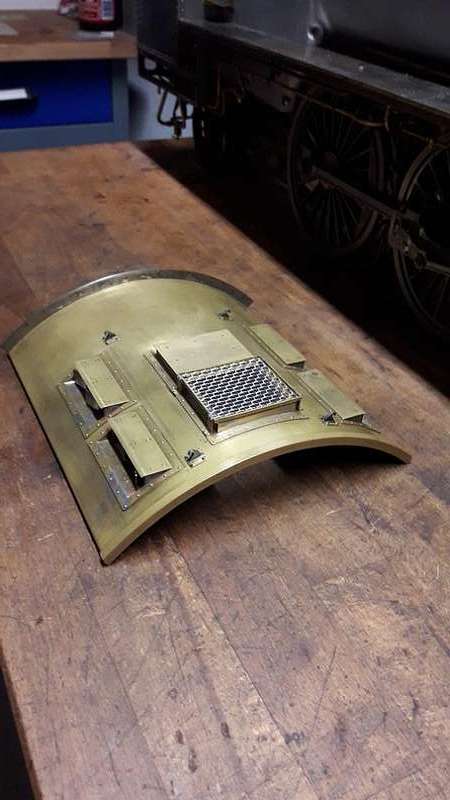
Ich wollte das der Führerstand von oben zugänglich ist um besser zu sehen was man macht beim heizen etc.. Weiter soll auf der Konsole im hinteren Dachbereich Servos untergebracht werden für die Steuerung, die Zugänglichkeit ist daher wichtig.
20201115_175406 (Steffel)
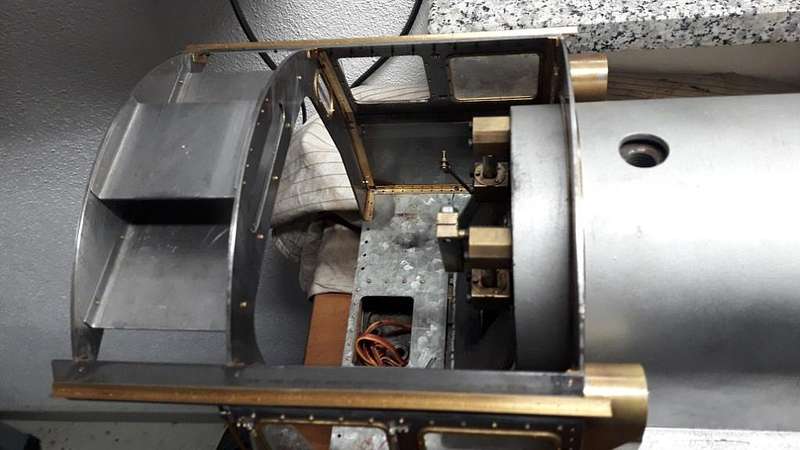
Einen weiteren Gedanken konnte ich auch umsetzen, ein Holzdach. Ich war immer wieder hin-hergerissen ob Stahl bzw. allgemein Metall nicht doch besser wäre wegen Verzug etc.. Ich habe mich dann doch für Holz entschieden da ich hätte eine Rollmaschine für 3mm Blech bauen müssen bzw. mir den Zugang zu einer versorgen. Irgendwie erschien mir dann die Holzvariante einfacher und es entsprach dem Original.
20201115_175132 (Steffel)
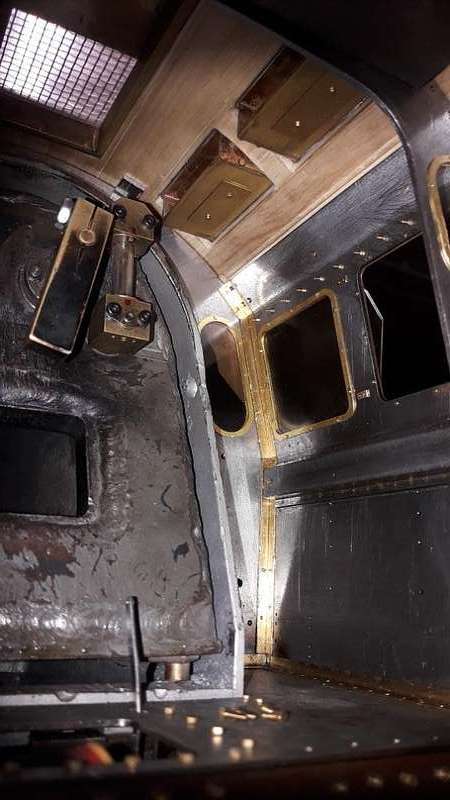
Die Frage war nun wie das gewölbte Holzdach herstellen?
Sperrholz nehmen und mit Feuchtigkeit und Wärme biegen?
Diese Variante schied aus da ich darin keine Erfahrung hatte und ich Bedenken hatte das diese Konstruktion sich im Betrieb weiter verzieht und das Dach flügelig wird.
Mehrer Schichten Furnier über eine Matritze übereinander kleben?
Auch diese Variante schied aus, weil ich darin keine Erfahrung hatte und der Bezug von Furnier unter 1mm mir knifflig erschien. Das Holzdach ist nur 3mm stark.
Leihmholz herstellen?
Das war letzlich die Idee welche ich umsetzte. Leimholz ist recht resistent gegen Verzug. Also holte ich mir auf dem Baumarkt Fichtenleisten 5x10mm, eine Siebdruck-Platte und ein Ø30 Rundholz.
Aus der Siebdruckplatte schnitt ich grob zwei Scheiben und bohrte diese. Anschließend habe ich das Rundholz mit Absätzen und Zentrierung versehen und mit den Siebdruckscheiben gefügt (Leim). Dann das Ganze dann auf die Drehmaschine und die Scheiben überdreht auf den Radius welcher innen vom Dach sein sollte.
20200822_211807 (Steffel)
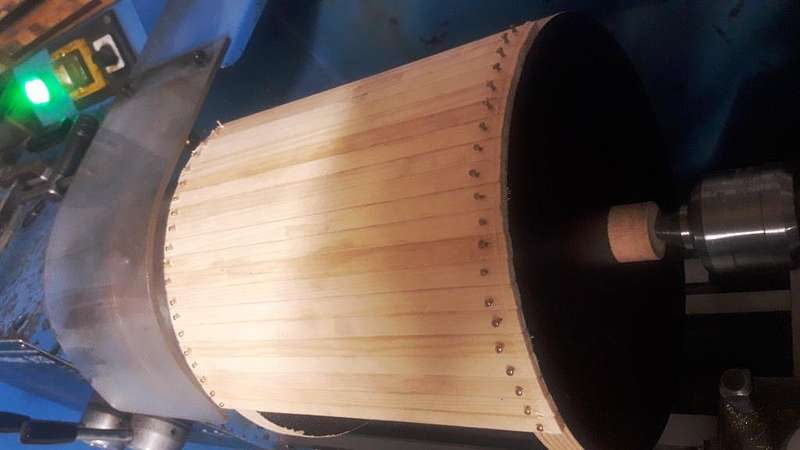
Die Holzleisten habe ich an der Seite über eine Vorrichtung auf der Fräse angeschrägt so das der Querschnitt ein Trapez ergab. Die Leisten habe ich dann aneinander und auf die Siebdruckscheiben aufgeklebt. Nach dem trocknen habe ich den Außendurchmesser überdreht. Dann zwischen den Platten herausgesägt und fertig war das Holzdach im gewünschten Radius und Stärke.
20200823_172156 (Steffel)
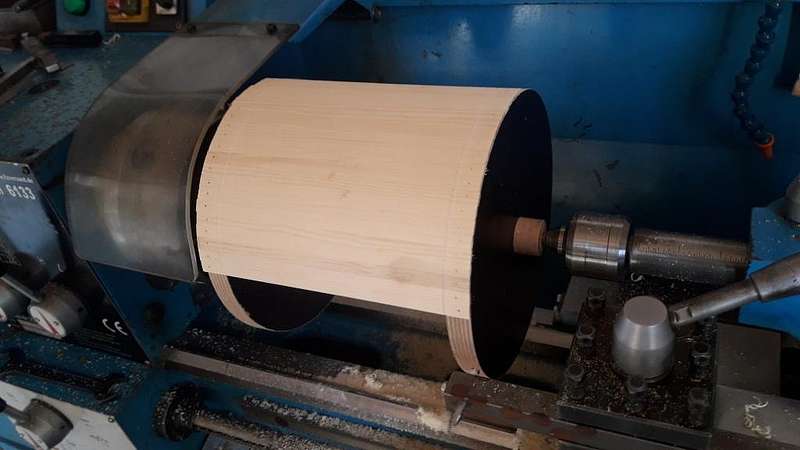
Nun wurde es wieder knifflig. Die Dachaufbauten mussten her. Am meisten haben mich die U-Profile an Vorder- und Hinterseite aufgehalten. Letztlich habe ich auch hier eine Siebdruckplatte gedreht welche den gewünschten Innenradius hatte. Durch einlegen von Blechstreifen in das U-Profil habe ich dann die Profile gebogen. Mit wärmen und Gedult habe ich es dann irgendwann hinbekommen. Die U-Profile und das angelötete Windblech am Dachende geben dem Dach unwahrscheinlich viel Steifigkeit.
Das Dachblech selbst habe ich auf einer weichen Unterlage und einem Rundmaterial eingerollt. Da es nur 0,5mm Blech ist lies sich dies sehr gut machen. Die Bohrungen für Nieten etc. habe ich vorher eingebracht.
Die restlichen Teile sind alles Dreh-Fräßteile welche ich alle weich (mit Flamme) in das Dachblech eingelötet habe.
Die restlichen Aufbauten sind zu großen Teilen nur Schneidteile welche gebohrt und miteinander gefügt sind.
20201007_201633 (Steffel)
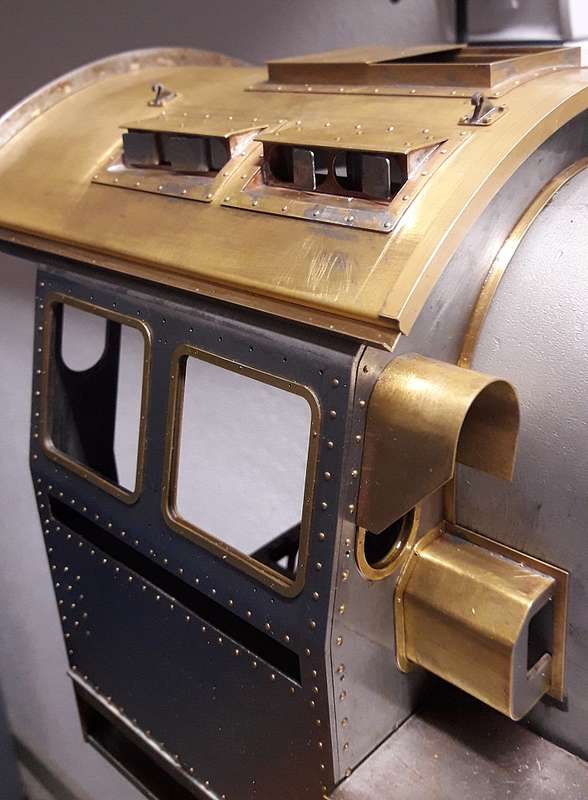
20201007_201840 (Steffel)
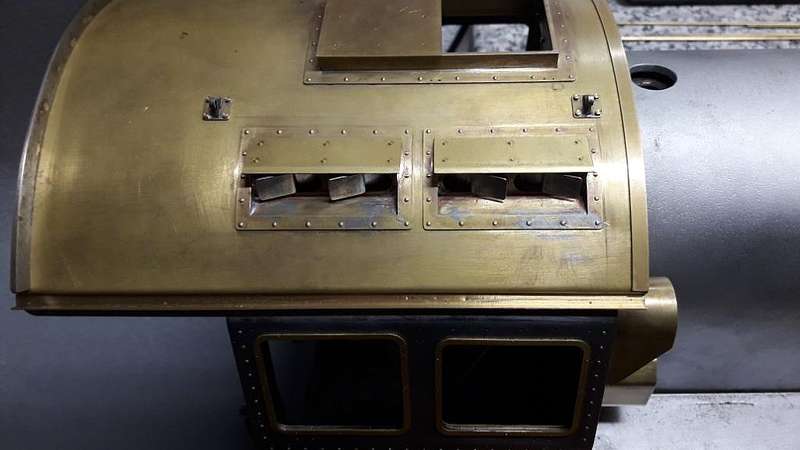
20201115_175043 (Steffel)
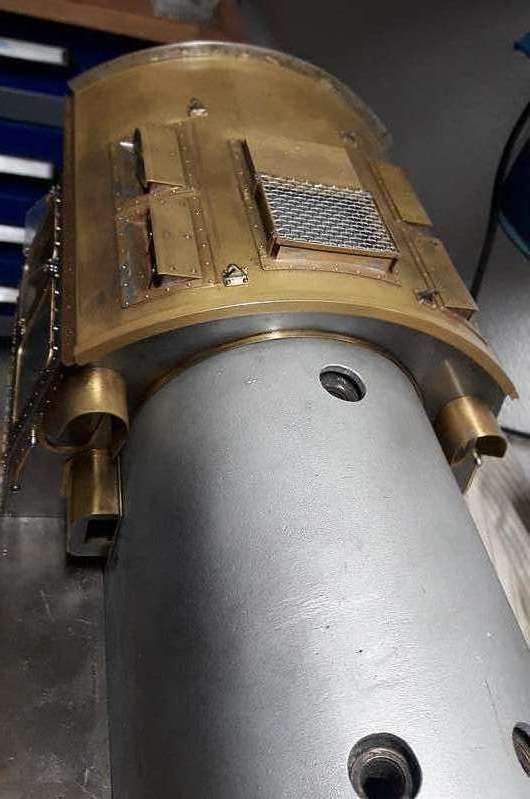
Mit dem Dach glaubte ich das Schwierigste geschafft zu haben.
Aber dem war nicht so.
Die Griffstangenfertigung lies sehr oft die fertigen Teile in den Schrottkübel wandern, da sie mich überhaupt nicht zufrieden stellten.
Als erste erörterte ich wie ich die Kugeln der Griffstangen herstellen sollte?
Einen Kugeldreher bauen bzw. Formmeißel fräsen/härten mit welchen die Kugel und das Haltestück aus einem Stück gefertigt werden kann?
Oder fertige Kugeln kaufen entsprechend Bohren und durch Löten fügen?
Ich entschied mich für den zweiten Gedanken.
Kugeln in allen gewünschten Größen (bei mir Ø4 und Ø3,5) bietet das Wälzlagersortiment. Allerdings sind diese auch schon gehärtet.
Blieb also nur der Versuch des Weichglühens. Hier schaute ich mir die Werkstoffe an, der klassische Wälzlagerstahl ist 1.3505 (100Cr6). Dieser lässt sich weichglühen aber nicht mit den häuslichen Mitteln. Ich habe es trotzdem versucht und bin natürlich kläglich gescheitert. Hier benötigt man einen Ofen welcher die Temperaturen halten kann bzw. diese über die Zeit langsam runter fährt.
Daher habe ich den Wälzlagerstahl für korrosive Anwendungen hergenommen. Dieser besteht aus dem Werkstoff 1.4034 (X46Cr13).
Wenn man hier in die Wärmebehandlung schaut sieht man das ein Weichglühen bei 750C° - 850°C erfolgen soll und die langsame Abkühlung im Ofen oder LUFT.
Daher habe ich die Kugeln kurz geglüht und dann langsam mit dem Brenner abgekühlt. Das ganze auf Schamotte diese hält schön die Wärme und verzögert den Prozess.
Das Ganze war von Erfolg gekrönt die Kugeln liesen sich anschließend mit üblichen Mitteln bohren, mit HSS-G, Co6/Co8-Bohrer und Zentrierbohrer. Immer noch fest aber machbar.
Nun mussten immer zwei Bohrungen in die Kugel welche genau 90° versetzt sein mussten.
Hier habe ich viel probiert und Lehrgeld bezahlt.
Letztlich hat sich die folgende Methode bewährt.
Alles auf der Drehbank fertigen im Dreibackenfutter, bei der ersten Bohrung zentriert dieses schön die Kugel. (Achtung nicht zu fest spannen sonst gibts es schnell Druckstellen).
Bei der zweiten Bohrung muss die erste Bohrung entgradet werden (meist ist kein Grad) und auf eine Backe gestellt werden. Dadurch kommt der 90° Winkel, aber Obacht, es muss ein Blech beigelgt werden welches den fehlenden Kugelteil in der Höhe ersetzt. Bei den Kugeln Ø3,5 waren es 0,2mm. Wenn man das nicht tut, schaut es einfach nicht mittig und damit unschön aus.
Wenn man genau hinschaut sieht man im Bild das untergeschobene Blech.
20201115_151533 (Steffel)
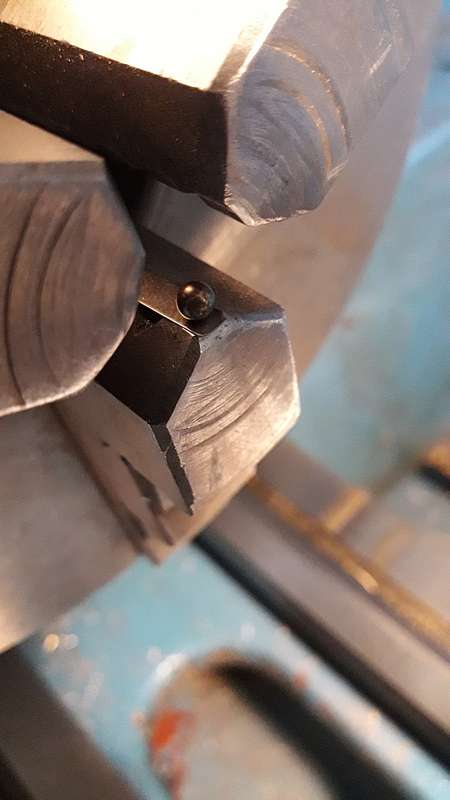
Anschließend habe ich die Abstandshalter aus Ø1,5 gefertigt und mit M1 Gewinde (innen) versehen. Das ging mittels Spannzange dann wieder ganz einfach. Das Löten wurde dann wieder etwas anspruchsvoller.
Ich Esel habe erst alle Abstandshalter auf eine Grunplatte aufgeschraubt (welche das Lochbild wiedergab wie am Führerstand) und die Griffstange montiert. Dann wollte ich die Abstandshalter mit den Kugeln und den Griffstangen gleichzeitig verlöten. Das musste natürlich scheitern weil die Wärmeinbringung das Messing ausdehnt und alles verschob.
Löten mit scharfer kurzer Flame brachte hier Abhilfe allerdings wurden die Abstandshalter nicht so recht warm weil diese mit der Grundplatte verschraubt waren was wiederum zu nicht brauchbaren Lötungen führte und die Produkte damit in den Schrottkasten gingen.
Anmerkung: bei der hiesigen Lötung ist immer hartes Löten gemeint da Weichlöten durch den hochlegierten Stahl nicht funktioniert. Zumindesten ist das meine Erfahrung.
Daher siegte dann die Einsicht die Abstandshalter mit den Kugeln alleinig zu verlöten. Und die Griffstangen dann nur einzuschieben und ggf. mit Kleber zu fixieren. Letzlich brauchte es keinen Kleber, die Griffstangen sitzen straff genug. Und das Ganze hat noch einen Charm, wenn mal die Stange verbogen wird reicht ggf. nur der Austausch der Griffstange, Kugeln und Abstandshalter können Wiederverwendung finden.
Das Löten der Abstandhalter habe ich dann gelöst indem ich als Anschlag die Griffstange einschob und danach den Abstandshalter. Vorher Lötpaste mit Lotanteil, weil Zugabe mit Stab wird nix (zumindestens bin ich dafür zu ungeschickt).
Damit sich nichts verrüttelt etc. habe ich in den Schamottestein eine Bohrung gemacht und die Kugel mit gefügten Abstandshalter eingesetzt (unten im Bild sieht man rechts einen fertigen Halter welcher noch in der Bohrung steckt, links ist jender fertig und muss noch geputzt werden).
Anschließend die Kugel erwärmt, dabei wird auch der Abstandshalter ausreichend durchgewärmt und das Lot sucht sich seinen Weg.
Mit den Ergebnissen konnte ich leben. Hier und da musste ein Halter mal nachgerichtet werden indem ich den Abstandshalter in eine passene Bohrung gesteckt und mit der Kugel und einen Bohrer in der Bohrung der Griffstange, nachgerichtet habe.
Mit den dann folgenden Ergebnissen war ich zufrieden, somit landeten die Griffstangen nicht im Schrott sondern am Führerstand.
20201115_144039 (Steffel)
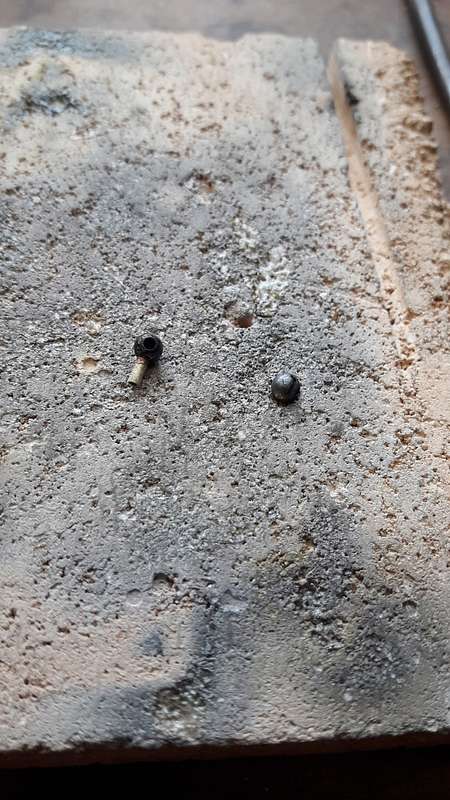
20201115_175031 (Steffel)
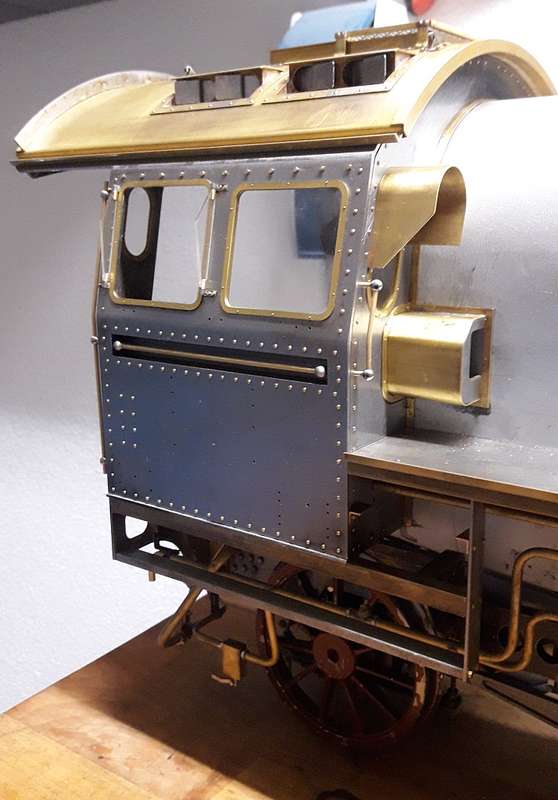
20201115_175102 (Steffel)
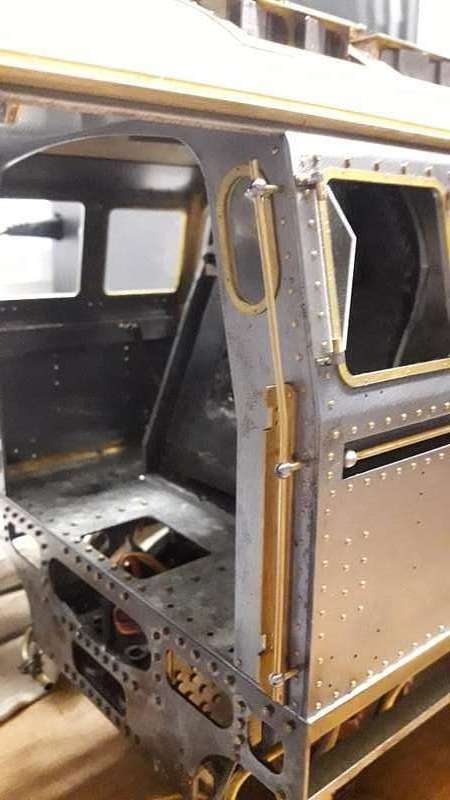
20201115_175203 (Steffel)
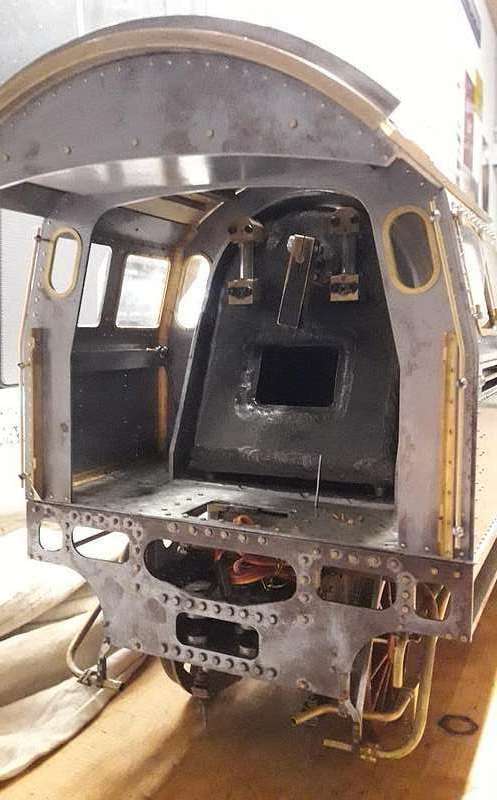
Die Bilder zeigen auch das ringsherum die Fenster drinn sind. Diese habe ich aus 1,5mm Plexiglass gemacht ich hoffe sie halten die Wärmeeinwirkung vom Kessel ab.
20201115_175237 (Steffel)
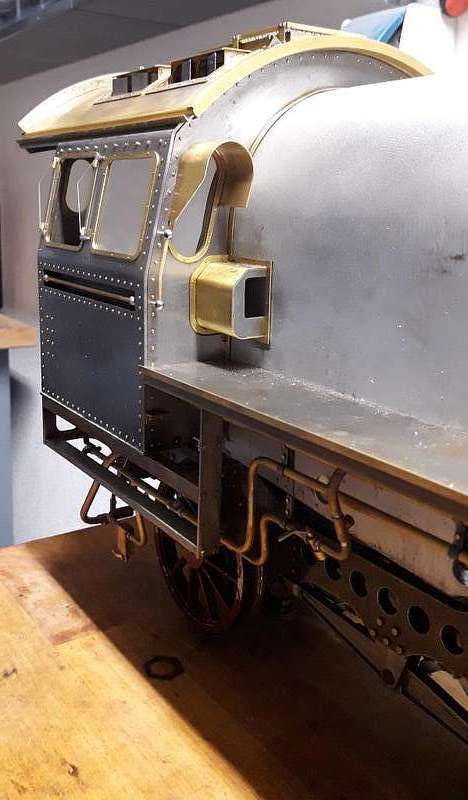
20201115_175328 (Steffel)
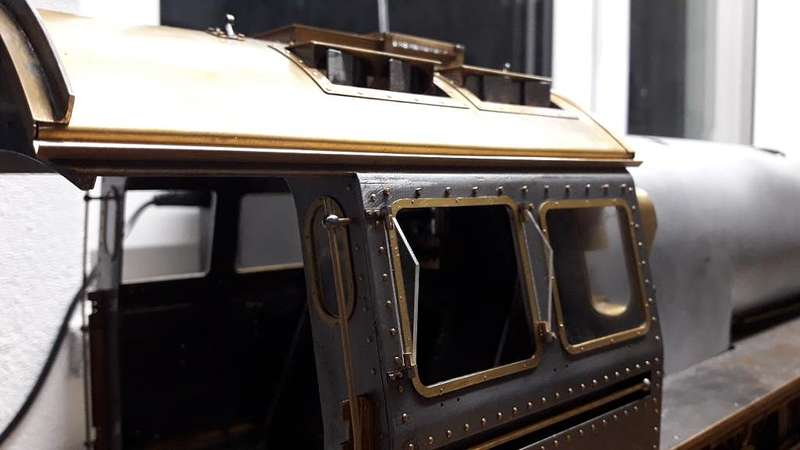
20201115_175220 (Steffel)
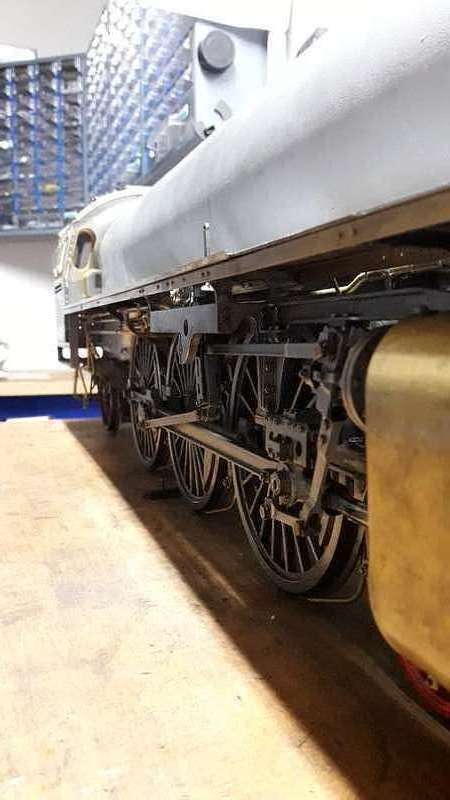
20201115_175304 (Steffel)
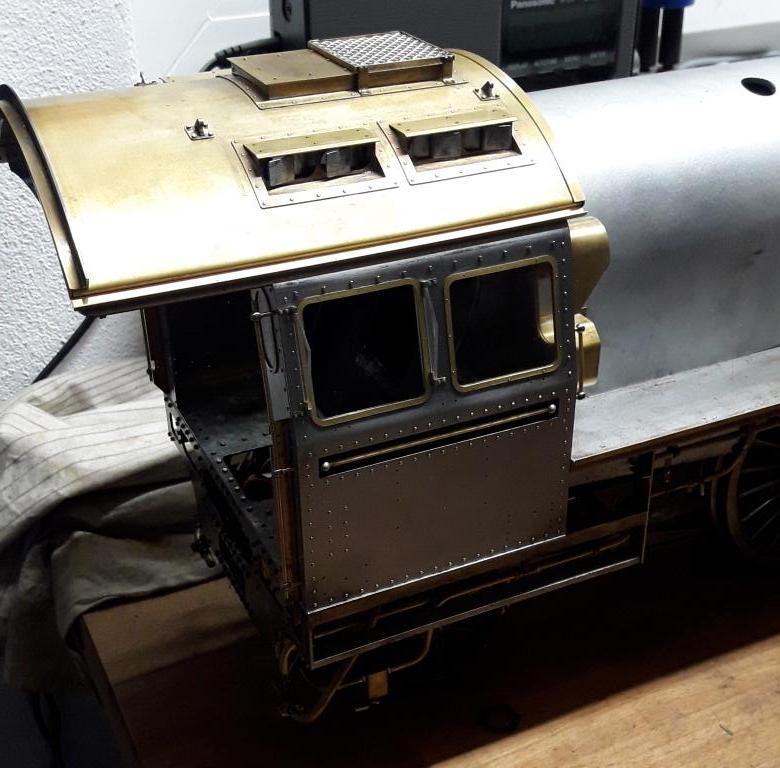
Als nächstes stehen jetzt die Türen an und die Abstandshalter für die Schilder. Dann noch die Verkleidung im Führerstand. Und dann muss ich erstmal weiter konstruieren.
Abschließende kann ich nur sagen, die Konstruktion in 3D gemacht zu haben war der richtigste Weg, anders wäre das warhscheinlich so nichts geworden, gerade die Partie Dach wäre mit Sicherheit so nicht umzusetzen gewesen. Hut ab wer es trotzdem ohne solch Leistungsstarker Mittel kann.
Beste Grüße