Als Lösung kam für mich nur eine Zwischenplatte in Frage. Diese hat Gewindebohrungen mit Grund von unten um mit dem Unterbau verschraubt zu werden und Rundringe zur Abdichtung. Von oben sind ebenfalls Gewindebohrungen welche den Maschinenfuß zur Befestigung dienen.
Fu_1 (Steffel)
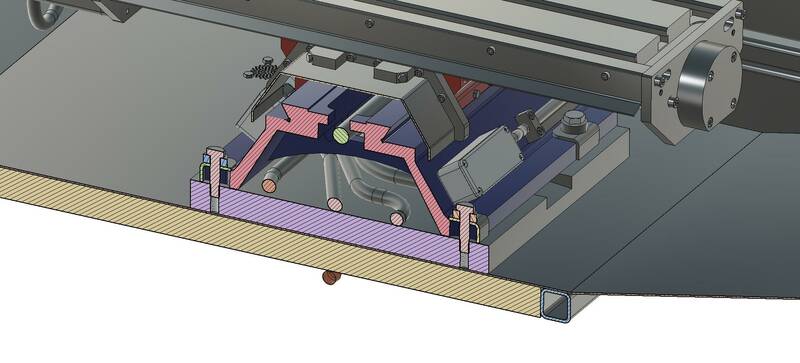
Fu_2 (Steffel)
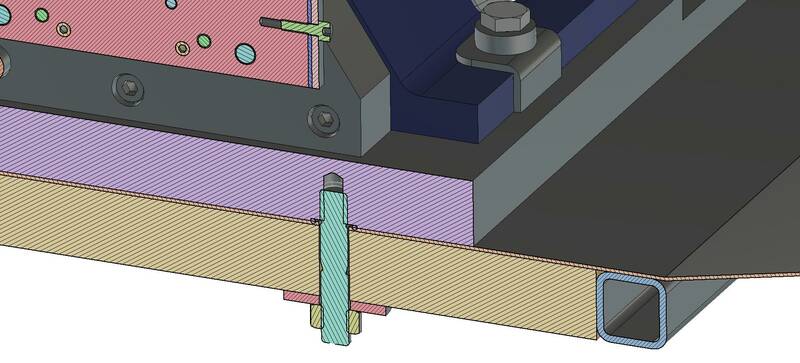
Die Zwischenplatte ist 300x235x30 abzüglich der überfräsen Fläche oben und unten. Auch den Maschinenfuß habe ich auf der Aufstandsfläche nochmal plan gefräst.
Hier musste ich auch dazulernen, das Planfräsen in mehreren Schnitten nebeneinander selbst mit nur 0,1mm Zustellung im letzten Span mit 60mm Messerkopf, allein für den Werkzeugmaschinenbau, nicht ausreichend ist.
Wenn ich beide Komponenten gefügt habe kippelte der Fuß leicht. Mit der Messuhr waren 0,05mm Kippeln sichtbar. Beim festziehen der Fußschrauben verzog es den Fuß und damit die Führung von y. Das konnte ich so nicht lassen. Da mir Schleifwerkzeuge oder Bohrwerk in der Größe, das man in einem Schnitt über die Fläche gehen könnte, nicht zugänglich ist, habe ich beide Flächen Gussfuß und Stahlplatte eben geschabt.
Bei der Stahlplatte habe ich ziemlich lange gebraucht da einfach der Werkstoff recht zäh ist für das Schaben. Darum sieht man auf einigen Bildern das die Platte noch blau lackiert ist und später blank mit dem Schabmuster. Am Ende muss ich sagen, hat sich der Aufwand gelohnt. Der Fuß sitzt satt auf und kann ohne Angst vor Verspannung festgezogen werden. Durch die zusätzliche Massenkopplung werden ggf. auch Resonanzen unterbunden und die Steifigkeit nimmt etwas zu.
Ich habe zwischen die Flächen etwas Öl gegeben um Korrosionen vorzubeugen. Der Maschinenfuß hat seitlich die typisch halboffenen Bohrungen um eine seitliche Verschiebbarkeit zu gewähren. Leider sammelen sich in diesen immer die Späne etc.. Darum habe ich abgewinkelte Bleche unter die Schrauben eingebaut um dem vorzubeugen.
Eine weitere Abdichtproblematik ereilte mich zum Thema Kabeleinführung und Kühlemulsionszuführung in den abgedichteten Arbeitsraum.
Da ich nicht von außen über die Einhausung hinweg und dann von oben an die Fräse die Medien ranführen wollte, was mir optisch nicht gefallen hätte, blieb nur von unten durch die Wanne gehen und diesen Anschluss dicht zu gestalten.
Da ich sowieso mit einer Medienkette vom feststehenden Teil zum beweglichen Fräskopf übergehen wollte brauchte die Kette einen Festpunkt am Grundkörper.
Da baulich nichts vorhanden war stellte ich eine Kabelsäule neben die Maschine aus 40x80x4 Kastenprofil. Mit einer dicht verschweißten Stirnplatte und einer Gegenbrille verschraubte ich diese gegen den Unterbau. Der obere Flansch ist gegen die Wanne mit Getriebedichtmittel abgedichtet, da ein zukünftiges lösen eher unwahrscheinlich ist. Die Kabelsäule ist so hoch das Kühlemulsion eher zur Tür hinausläuft bevor diese in die Kabelsäule von oben hineinlaufen kann.
Später habe ich mich etwas geärgert. Statt die Kabelsäule auf dem Wannenblech aufzusetzen hätte ich die Grundplatte in dem Bereich auskragen lassen sollen, mit einem Durchbruch um die Kabelsäule mit auf die große Grundplatte stellen zu können.
Denn durch die getrennten Komponenten und der kleinen Aufstandsfläche steht die Kabelsäule schnell schief zur Maschine und es muss mit Gegenmaßnahmen beigegangen werden, dies wäre bei einer Montage auf der großen Grundplatte nicht passiert.
Kabel_1 (Steffel)
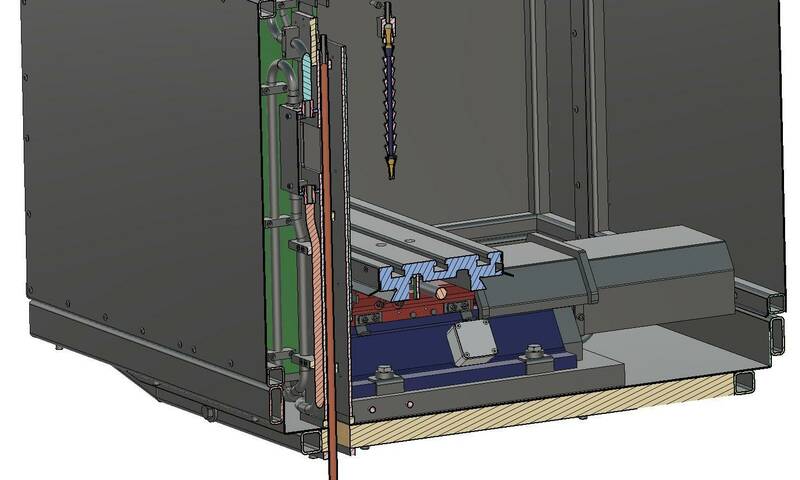
Kabel_2 (Steffel)
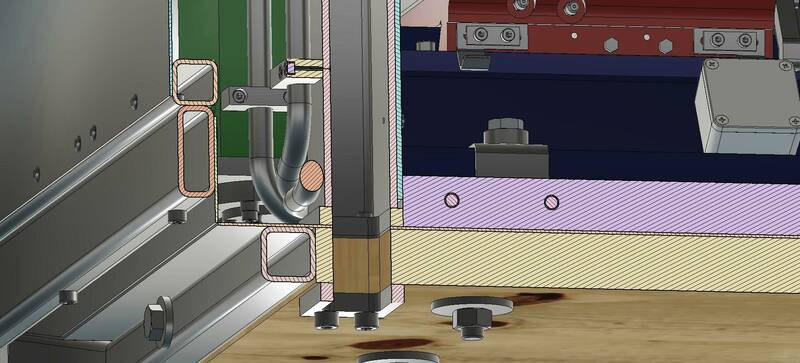
An der Kabeläule konnte ich sehr gut die Energiekette befestigend und die zugehörigen Medien in Ihr nach oben führen und verteilen. Auch der Vorlauf der Kühlemulsion führt in dieser lang und geht bei der Energiekette in einem Schlauch weiter.
Hier offenbarte sich bei der Montage ein Konstruktionsfehler.
Ich habe die Energiekette bei IGUS bezogen. Diese bitten ein sehr schönes Baukastensystem an. Ich habe mir, die nach meinem Verständnis passende Kette, herausgesucht das 3D-Modell dazu und in mein Gesamtmodell hineinprojiziert. Soweit hat alles gepasst. Was ich missachtet habe ist die Rückstellkraft des Kühlemulsionsschläuche und der Kabel wenn diese nahe den Mindestbiegeradien sind. Die kleine Kette ist nicht steif genug um diese Kräfte aufzunehmen und verformt sich entsprechend. Ich musste daher einen sehr weichen Kühlmittelschlauch nehmen sonst hätte ich nochmal alles umbauen müssen. Sollte ich nochmal in die konstruktive Situation geraden würde ich den größtmöglichen Radius, den der Bauraum hergibt, verwenden.
Die Kühlmittelpumpe steht im Unterschrank und fördert über eine Steigleitung die Kühlemulsion nach oben. Zum Drosseln ist ein Kugelhahn eingebaut, da dieser an der Rückwand des Schrankes ist musste ich die Betätigung mittels Stange nach vorn verlängern. Somit kann ich von außen den Kühlmittelstrom regeln.
Die Praxis zeigt aber das bei längern laufen lassen der Motor sehr heiß wird. Ich muss mal schauen ob ich den Emulsionsvorlauf mittels Kühlschlangen um den Motor gewunden bekomme oder Kühlrippen welche mit Emulsion durchflossen werden können.
Ggf. tausche ich auch einfach die Pumpe gegen ein Produkt was eine Einschaltdauer von 100% hat.
Kuehlung_Pumpe (Steffel)

Kuehlung_hinten (Steffel)
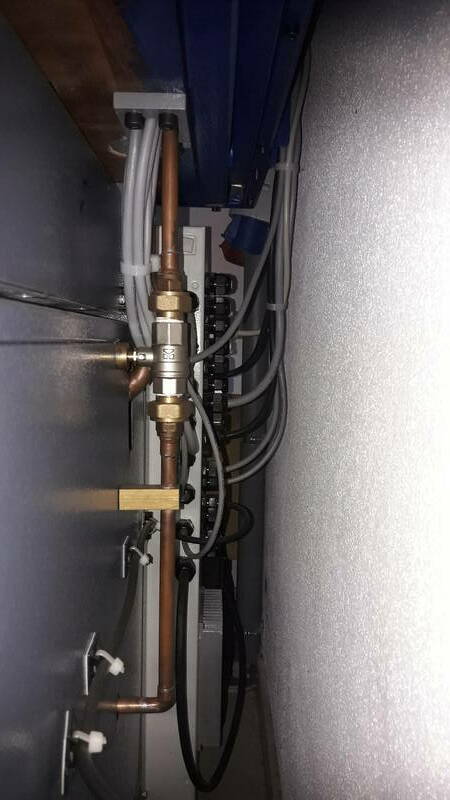
Der Kühlmittelablauf ist relativ einfach. Hier habe ich in das Wannenblech kleine Löcher gebohrt (Sieb) und von unten einen Sammler gegengeschraubt. Mittels Rundging dichtet dieser gegen das Wannenblech ab. Ein Rohr mit Verschraubung führt dann zurück zum Kühlmittelbehälter im Unterschrank.
K_hlung_Ablauf (Steffel)
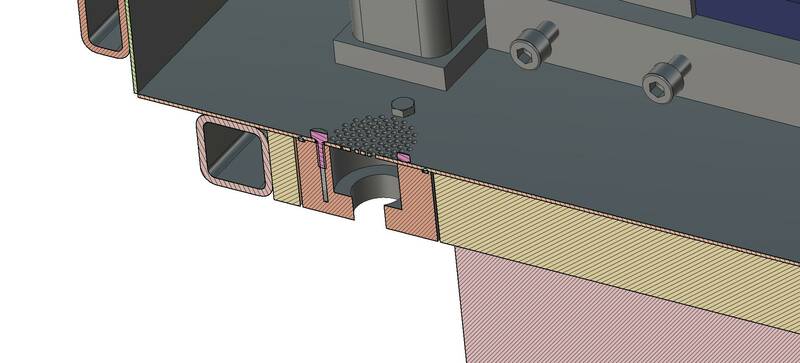
Die Kabelsäule dient auch um die Kabelführung der Maschine zu ordnen. Mir war es wichtig das keine Kabel von Schrittmotoren oder Sensoren in der Wanne rumliegen, dort beschädigt werden bzw. beim Reinigen im weg sind. Darum habe ich versucht alle Kabel im/unter dem Maschinenfuß zu verlegen. Die große Grundplatte habe ich mit einer größeren Nut versehen um unter dem Fuß der Maschine hindurchtauchen zu können.
Kabel_5 (Steffel)
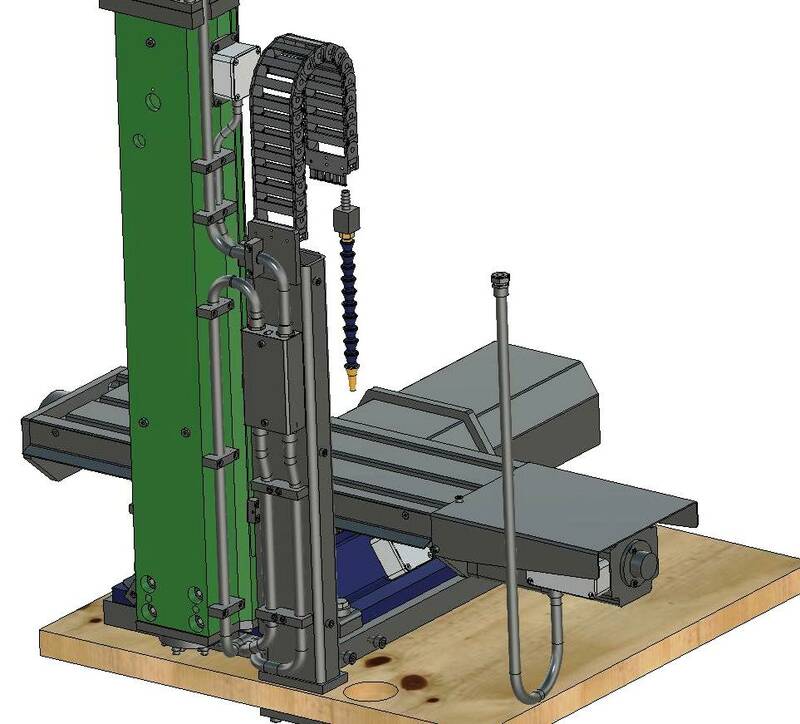
Kabel_4 (Steffel)
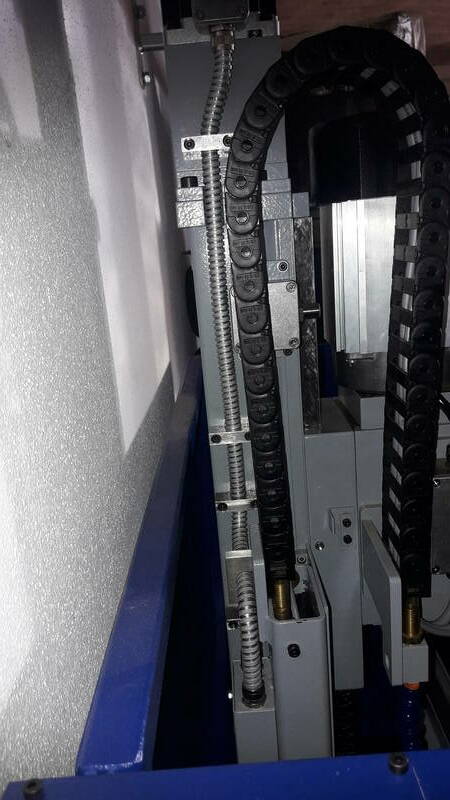
Alle Kabel sind in Metallschutzschläuchen von HellermannTyton verlegt, die Metallschutzschläuche kann man mit Verschraubungen versehen so dass man mit Mutter oder direkt mit Gewindebohrungen die Anschlüsse gestalten kann.
Vor der Montage empfiehlt es sich einen Fädelstrick zu montieren um später die Kabel durchzuziehen.
An der Z-Säule und der Kabelsäule sind die Metallschutzschläuche mit eigens gefertigten Aluklemmen sauber befestigt. Das schaut ordentliche aus und verhindert Scheuerstellen.
Kabel_6 (Steffel)
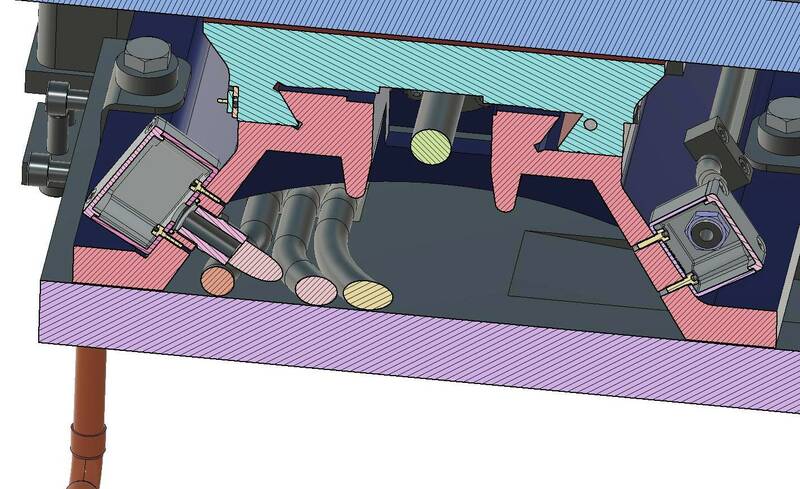
Kabel_7 (Steffel)
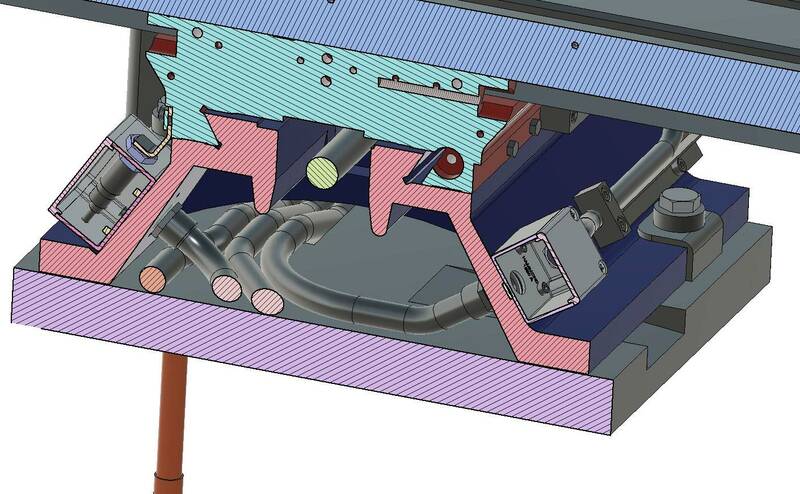
An der Y und Z Achse sind als Endschalter Induktive Näherungssensoren. Diese sind in Metallkästen von Hammond Electronics. Entweder werden die Kabel von hinten eingeführt und mit Rundringen abgedichtet oder per Verschraubung direkt in die Gehäuse.
Besonders knifflig war die Kabelführung zu dem Endschalter der X-Achse.
Der Übergang vom festen zu beweglichen Teil war nicht ohne weil Platz für eine Energiekette etc. nicht reichte.
Kabel_8 (Steffel)
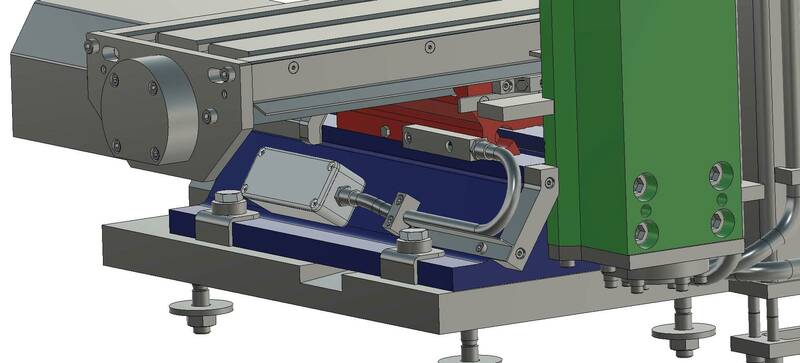
Letztlich habe ich das Metallschutzrohr selbst als kleine Energiekette genutzt. Im Kreuzsupport wurde dann eine Querborhung eingebracht um das Kabel des Sensors aufzunehmen.
Kabel_9 (Steffel)
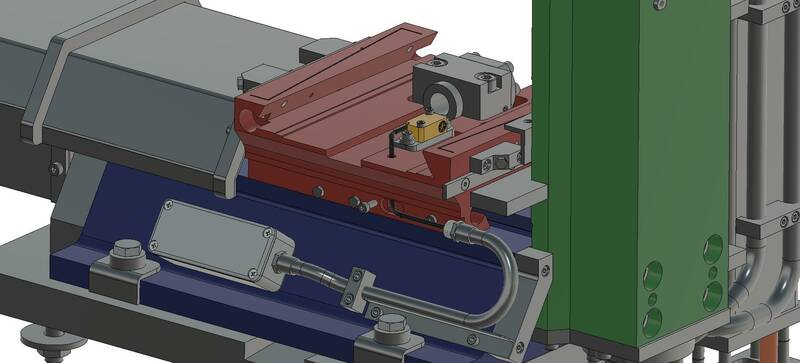
Ich habe für die Endlagenabfrage der X und Y Achse immer einem Sensor und zwei Fahnen. Bei Y – sind dies einfach gekantet Blechfahnen mit einem großen Langloch und einer Deckscheibe um große Einstellbarkeit zu gewährleisten.
Bei der Z-Achse ist es nur eine Fahne Begrenzung nach oben.
Bei der X – Achse war der beenget Bauraum ein riesen Problem.
Letztlich habe ich in den Frästisch von unten Nuten gefertigt und verschiebbare Endschalterfahnen montiert. Da nur 2-3 mm Schaltabstand sind muss es auch genau zugehen. Zusätzlich habe ich den Sensor auf eine Grundplatte montiert welche in der Tiefe verstellbar ist um den Schaltabstand einstellen zu können. Da die Fahnen den Sensor queren würde bei einer Kollision es den Sensor abscheren.
Fraestisch_1 (Steffel)
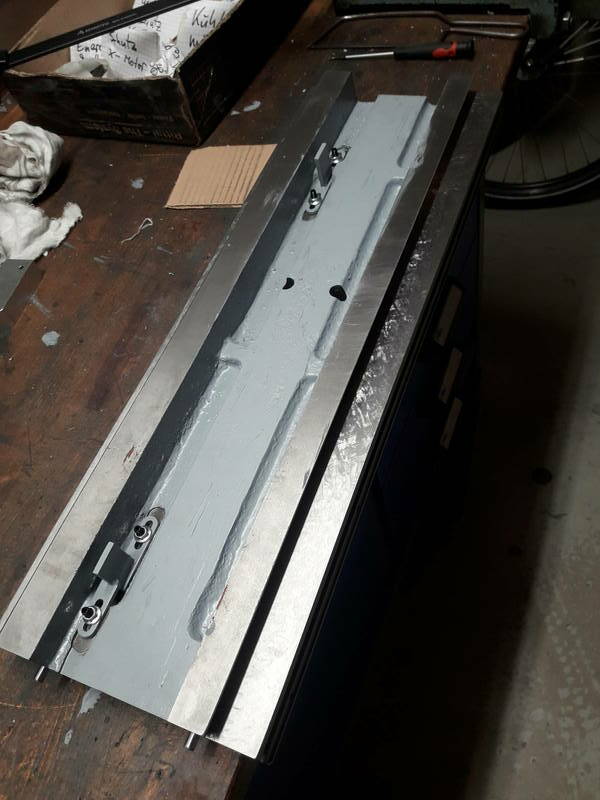
Fraestisch_2 (Steffel)
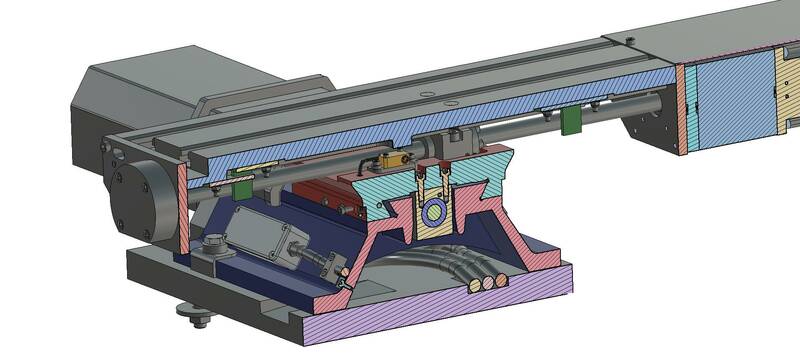
Damit wären erstmal alle Konstruktiven Merkmale der Maschine vorgestellte.