Hallo Buntbahner,
ich unterhielt mich mit Volker und wir sprachen darüber was mindestens so alles in einer Pförtnerloge vorhanden sein sollte.
Dabei stellten wir vorrangig fest, ein Stuhl wäre nicht schlecht.
Ich besitze noch einen wirklich uralten einfachen Holzstuhl und schlug vor so einen zu bauen.
Dann kam Volker mit dem Drehstuhl und meinte so etwas hätte er gern aber sehr Vorbild gerecht, nur könne er im Moment nicht sagen wie er so etwas selbst bauen könnte.
Meine Aussage war, natürlich könnte man so etwas bauen und ich sehe da auch kein Problem mit.
Hinzu kam bei mir die Tatsache, dass ich auch für mich selbst, Interesse an solch einem Drehstuhl entwickelte.
Ich bat deshalb Volker, erst einmal Bilder zu sammeln und den Stuhl in einfachen Ansichten zu zeichnen.
Kurze Zeit später hatte ich Bilder und Zeichnungen und aus dem PDF generierte ich die Fräsdateien für einen Übungsstuhl.
Wie üblich kam bei mir erst einmal Messing zum Einsatz, da sich dieses Material besonders gut verarbeiten lässt.
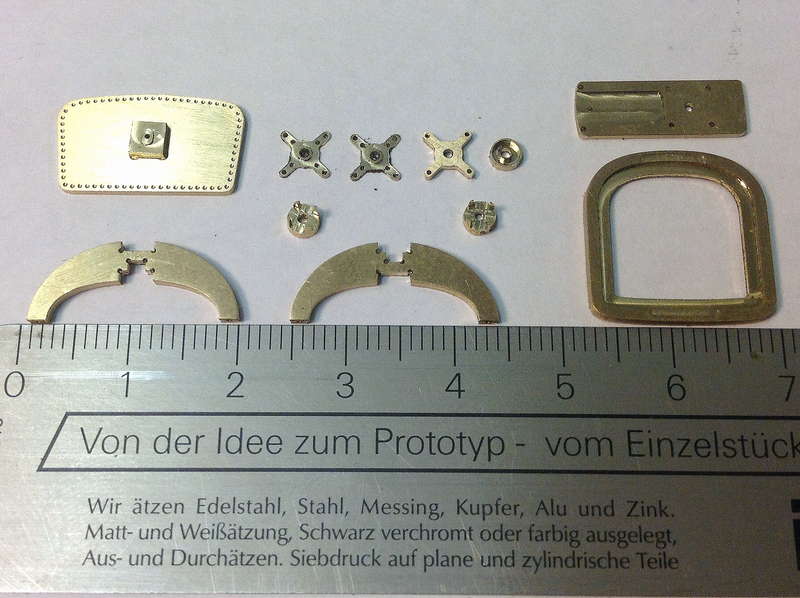
Erste Teile für einen Drehstuhl.
Dieses waren die ersten Teile die ich erstellte und Volker präsentieren konnte.
Da es ein Übungsstuhl ist, stellten wir fest, dass das mit der Rückenlehne muss noch besser werden muss.
Deshalb konzentrierten Volkers Gedanken und mein Tun auch erst einmal auf die Rückenlehne.
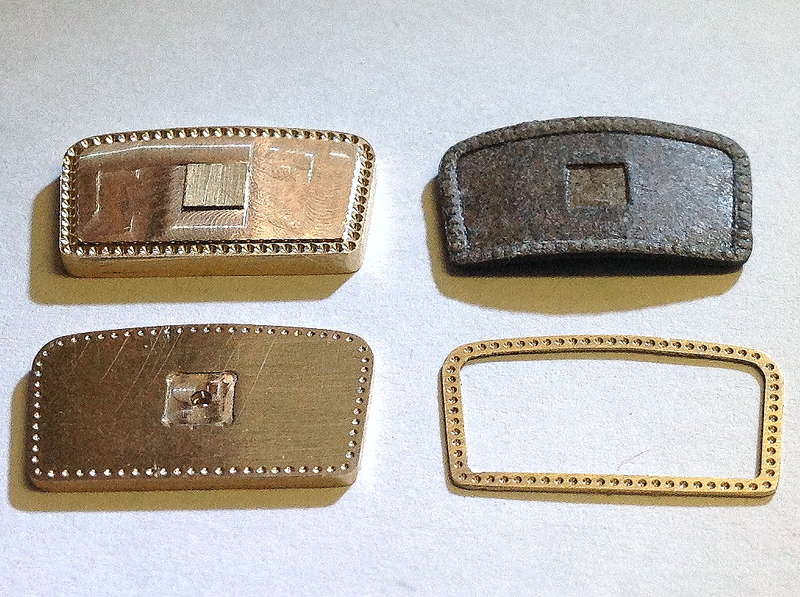
Entwicklung und Entstehung der Rückenlehne.
Unten Links die erste Übung der Rückenlehne, dabei wurden die Polsterziernägel als Anbohrungen eingebracht.
Da aber auch noch der umgelegte Sitzbezug fehlte, fräste ich einen Rahmen, um dieses besser nachbilden zu können.
Nur auch hier schauten die Polsterziernägel auch noch nicht überzeugend aus.
Dann schlug Volker vor, eine Patrize zu nutzen, das war besser denn jetzt mussten die Nägel ja nur noch negativ dargestellt werden.
Heraus kam dabei die Patrize oben links und der Abdruck davon oben rechts.
Den Abdruck von der Patrize habe ich mit 2 mm Graupappe gemacht.
Dazu habe beides einfach in einen Schraubstock mit glatten Backen gespannt und die Graupappe auf ca. 1 mm komprimiert.
Anschließend habe ich mit einem scharfen Messer die Rückenlehne um die Patrize herum ausgeschnitten.
Die Rückenlehne konnte ich jetzt in Form biegen und anschließend wurde diese mit Sekundenkleber getränkt und dadurch gefestigt.
Nach dem Trocken konnte die Graupappe in Form geschliffen werden.
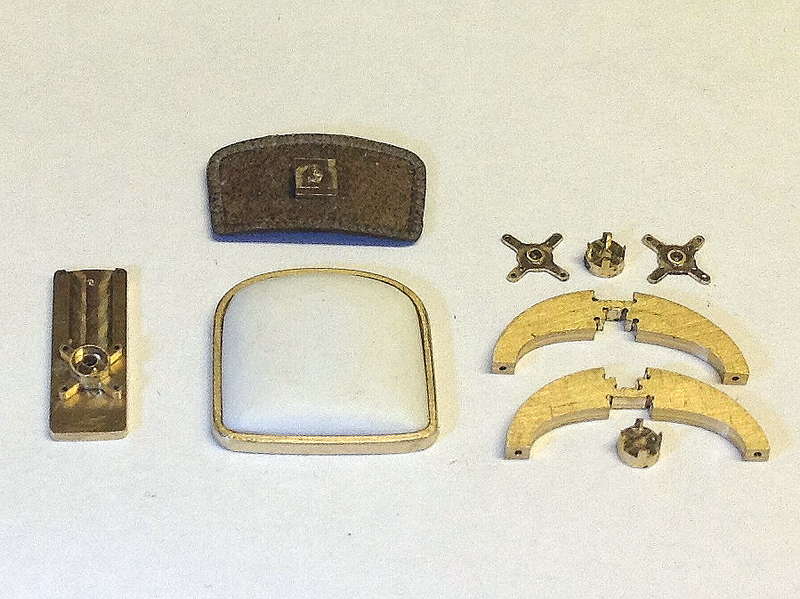
Erste Zusammenstellung der inzwischen gelungenen Drehstuhlteile.
Der Sitz wurde aus einer 2 mm Polystyrol-Platte in Form geschliffen.
So schauten die Teile für den Drehstuhl danach aus und hinzu gekommen war auch noch ein Sitzpolster das aus einem zu recht geschliffenem 2 mm Polystyrol-Stück entstand.
Es fehlten aber noch weitere Teile die jetzt gefertigt werden konnten.
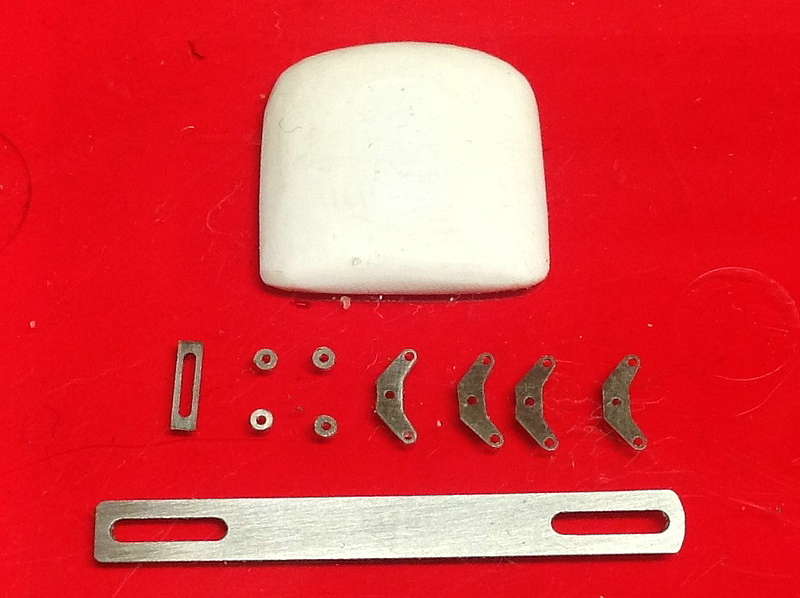
Sitzfläche, Federhaltebügel, Drehlagerscheibe, Rollenhalter und Rückenfeder wobei die Schlitze noch zu breit sind.
Hier zusehen noch einmal das Sitzpolster, außerdem Federhaltebügel, Drehlagerscheibe, Rollenhalter und Rückenfeder.
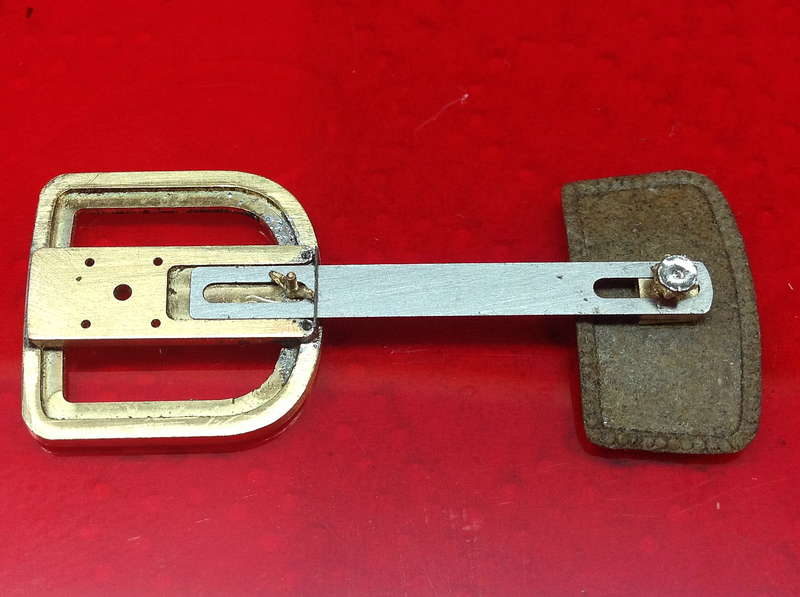
Dann konnten der Sitz und die Rückenlehne erstmalig zur Probe mit der Rückenfeder verbunden werden.
Auf die Herstellung der richtig funktionierenden Schraube und Flügelmutter gehe ich noch gesondert ein.
Leider stellte sich heraus, dass die Schlitze in Rückenfeder noch zu breit waren und mit der Schraube und Flügelmutter keine ausreichende Klemmung erreicht werden konnte.
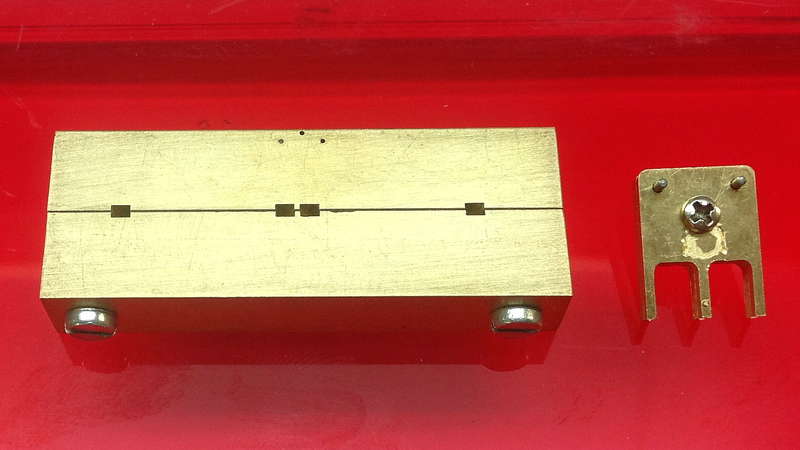
Links Bohrlehre für die Rollen-Befestigung in den Stuhlbeinen.
Die 3 Bohrungen an der Oberkannte dienen zum Halten beim Entgraten der Rollenhalter.
Rechts die Biegelehre für die Rollenhalter.
Jetzt beschäftigte ich mich mit den Rollen die ja schließlich drehbar und richtig rollen können sollten.
Die Rollenhalter hatte ich ja schon in der Abwinklung gezeigt.
Zum Biegen hatte ich mir eine Biegelehre erstellt.
Bei dem federharten Edelstahl ist aber kein scharfkantiges Abwinkeln möglich, ohne dass dieser bricht.
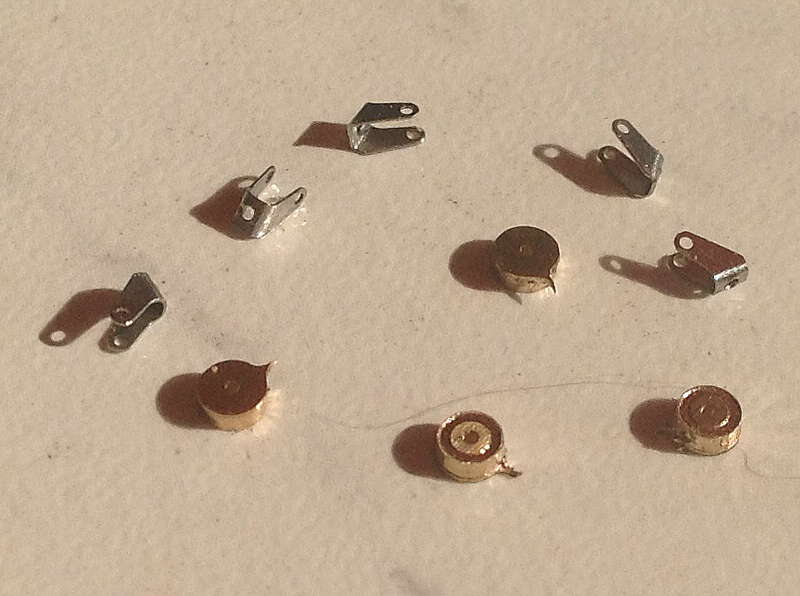
Die Rollenhalter sind mit der Biegelehre fertig gebogen.
Erste Probe Räder gefräst diesen müssen natürlich noch entgratet werden.
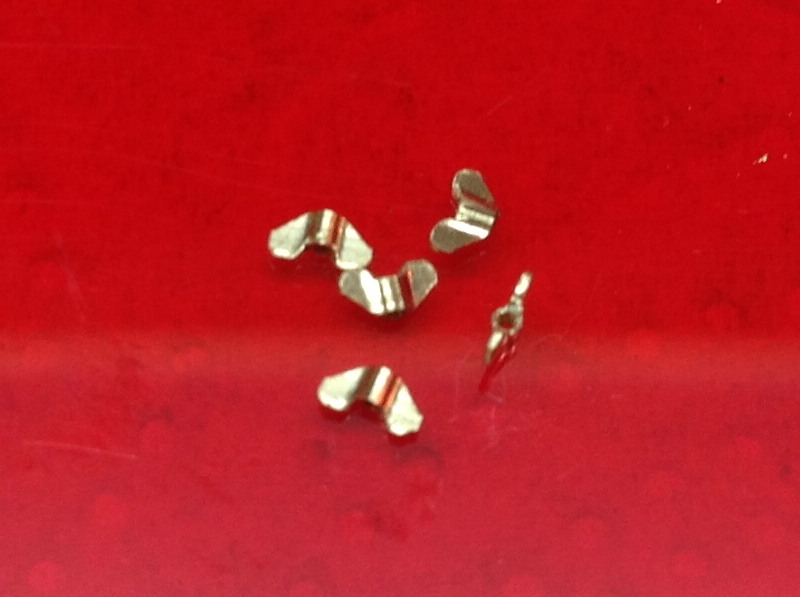
M 0,6 Flügelmuttern
Zur Erstellung der Flügelmuttern habe ich erst einmal eine 0,5 mm Bohrung in eine 2 mm Messingplatte eingebracht.
Dann habe ich mit einem 90° Stichel einen 3 mm Kreis um die Bohrung herum 1 mm tief gefräst.
Das ergab dann später die untere Schräge an der Flügelmutter.
Jetzt habe ich die Platte umgedreht um sie von der anderen Seite zu bearbeiten.
Als erstes wurde genau mittig über der 0,5 mm Bohrung eine kurze Bahn 1 mm tief mit eine 1 mm Fräser eingebracht.
Zum Schluss musste ich nur noch die Kontur der Flügelmutter ausfräsen.
Was jetzt noch fehlte waren die klassischen runden Flügel und das M 0,6 Gewinde.
Dazu habe ich einen M 0,6 Gewindebohrer genommen und begonnen das Gewinde zu schneiden.
Die Flügelmutter halte ich einfach zwischen den Fingern und dann kommt auch schnell der Moment, wo das Gewindeschneiden etwas schwererer geht.
Diesen Moment nutze ich aus um frei Hand, mit einer ganz feinen Diamant Trennscheibe, die Flügel rund zu schleifen.
Jetzt den Gewindebohrer vorsichtig zurück drehen, alles von den feinen Spänen befreien und anschließend das Gewinde fertig schneiden.