Da ich mit Kühlemulsion arbeiten will war mir der Schutz der Führungen und Schrittmotoren auch sehr wichtig. Daher haben alle Achsen Abtropfbleche und Schutze in jeglicher Art bekommen.
Bei der Y-Achse konnte ich über den vorderen Bereich einen Verschubschutz bauen. Im hinteren Bereich hatte ich ursprünglich einen Faltenbalk vorgesehen. Diesen wollte ich selber aus Teichfolie bauen. Die Teichfolie ist zum Einsatz gekommen aber das Falten habe ich gelassen ich habe einfach die Folie waagerecht montiert. Wenn die Y-Achse nach hinten fährt bildet die Folie von alleine einen angenehmen Bogen. An der Z-Achse habe ich im unteren Bereich den mit der Fräse gelieferten Faltenbalk wieder eingesetzt. In der Praxis zeigt sich das dieser doch etwas Schmutz an den nach innen gefalteten Stellen durchlässt. Daher werde ich noch eine Teichfolie davor installieren, welche breiter ist.
Schutz_1 (Steffel)
Schutz_2 (Steffel)
Schutz_3 (Steffel)
Bei der X – Achse habe ich über den Motor einfach ein gekantetes Blech gemacht. Die Seiten sind ebenfalls mit um 45° gekanteten Blechen vorn und hinten geschützt. Die Abdichtung zum Frästisch habe ich mit einer Rundschnur realisiert. Hierfür habe ich die vorhandene Nut genutzt welche im Frästisch für die linearen Skalenanzeigen vorgesehen sind. Was man in der Zeichnung nicht sieht. Bei der Montage war die Vorspannung durch den Rundschnur zu groß so dass ich ein 3mm breite Nut zusätzlich in die bestehende Nut gefertigt habe, um etwas tiefer zu kommen.
Schutz_4 (Steffel)
Schutz_5 (Steffel)
Im folgenden Bild sieht man die Maschine im Einsatz mit viel Kühlemulsion und wie sich alles verteilt. Da zeigen sich die Vorteile der Schutze und Ablaufbleche.
Das Werkstück ist übrigens der Dampfkasten von der Luftpumpe für die 03.
Schutz_6 (Steffel)
Um grundsätzlich mit Kühlemulsion zu arbeiten musste auch ein Gehäuse um die Maschine sein.
Von meiner großen konventionellen Fräse kenne ich die Problematik mit der Emulsion/Späne und deren Einwirkungen auf das Umfeld der Fräse. Da die CNC Fräse automatische Bewegungen ausführt verhindert eine Einhausung auch ungewollte Eingriffe in die Maschine.
Ich hatte mit der Konstruktion von Maschineneinhausungen bisher keine Erfahrung. Die Recherche brachte auch nicht viel ans Licht. Daher habe ich eigene Ideen verfolgt, dabei stand die eigene Fertigungsmöglichkeiten, Kosten und Gewicht im Vordergrund: das Grundgerüst sollte aus Kastenprofil entstehen, die Füllung mit Blechen.
Als Maschinenunterschrank dient ein Werkzeugschrank der Fa. Küpper. Da meine Werkbank und andere Schränke ebenfalls aus dem System sind bot sich dies an.
Die Werkbänke können bis 300kg belastet werden, ich wusste aber nicht ob ich eventuell diese Last überschreite. Die Maschine wog im Anlieferzustand ca.: 120kg. Das Schutzgehäuse habe ich mit 150kg vorkalkuliert, am Ende waren es 96kg. Die E-Technik, Kühleinrichtung und der ganze Kleinkram war ich damals geschätzt bei 400kg.
Daher musste eine Verstärkung des Schrankes erfolgen. Ich habe daher in alle vier Ecken jeweils senkrecht ein Kastenprofil eingebaut und mit der Blechverkleidung verschraubt. An der unteren Stirnseite des Kastenprofils habe ich Stirnplatten mit Gewinde eingeschweißt um Maschinenfüße mit Dämpfung verbauen zu können. Da fällt mir gerade auf die muss ich noch in der Richtigen Farbe lackieren.
Schrank_1 (Steffel)
Um das Kastenprofil einbauen zu können muss an den ursprünglichen Blechen Freigängigkeiten geschaffen werden. Das Führte dazu das trotz der massiven Holzplatte als Stirnplatte der Schrank freistehend nicht die nötige Steifigkeit gegen Torsion aufzeigte. Daher habe ich einen zusätzlichen Rahmen (Rahmeneck) aus 10x40 Flacheisen um die Türöffnung montier und mit den beiden vorderen Kastenprofilen und dem Schrank verschraubt. Nun war eine ausreichende Steifigkeit in allen Achsen gegeben.
Schrank_2 (Steffel)
Da ich nur ein Elektrodenschweißgerät, habe viel das Aufschweißen der Belche schon aus, da bei Bohrungen ausschweißen meist unschöne Nähte entstehen weil die Schlacke nicht weg kann. Hinzu kam die Gefahr dass sich alles verzieht oder wellig wird. Bei dem Grundgerüst um die Tischplatte habe ich Kastenprofil 30x30x3 gewählt. Der Äußere Rahmen ist aus 50x20x3. Der Aufsatzrahmen oben welcher die seitlichen Bleche Trägt besteht aus 25x25x2,5.
Die Stärke 2,5mm war gerade so die Grenze um mit Elektrode schweißen zu können.
Den unteren Rahmen begann ich um die Holzplatte herum zu konstruieren.
Rahmen_1 (Steffel)
Rahmen_2 (Steffel)
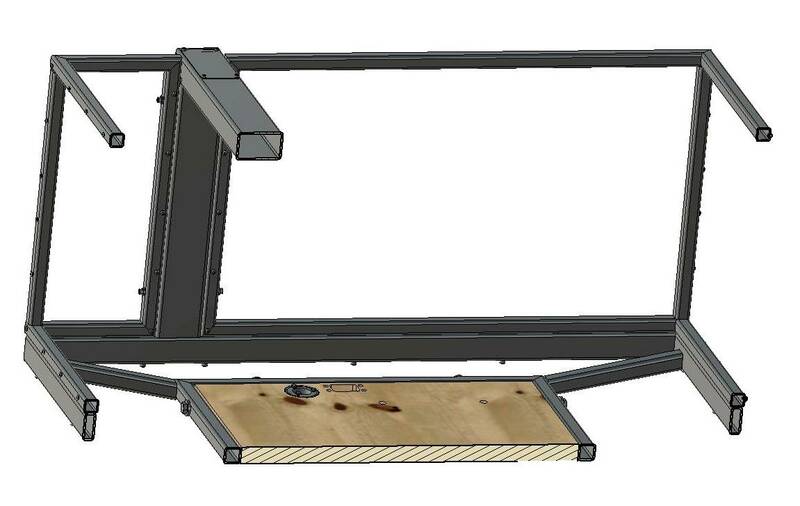
Die Befestigung an der Holzplatte erfolgt mit großen Holzschrauben und Spannhülsen damit der Kasten nicht zusammengedrückt wird.
Rahmen_3 (Steffel)
Ganz wichtig war mir das der obere Rahmen zum Teil abnehmbar ist um ggf. Reparaturen etc. an der Maschine ausführen zu können. Daher habe ich jeweils zwei Seitenteile abnehmbar gestaltet. Die Verbindung zum unteren Rahmen erfolgt mittels Schrauben und Senkblindnietmuttern.
Rahmen_4 (Steffel)
Rahmen_5 (Steffel)
Im Nachgang muss ich sagen wäre es wahrscheinlich besser gewesen statt der Holzplatte (Leimholz) eine Pertinaxplatte oder Stahlplatte zu verwenden. Letztere wäre sehr schwer was der Dämpfung zugutegekommen wäre aber auch sehr teuer.
Die Verkleidung des oberen Rahmen mit Blechen habe ich aus 1,5mm starken Blech gemacht. Dünner habe ich nicht gewagt da ich bedenken hatte das es wellig wird. Und eine Kantbank um eine Kreuzkantung zu erstellen habe ich in der Größe nicht bzw. keinen Zugang.
Die Befestigung am oberen Rahmen habe ich mit großen Blindnieten umgesetzt.
Verkleidung_1 (Steffel)
Die Wanne im unteren Rahmenbereich ist aus 1,5mm Blech. Diese ist links und rechts hochgekantet (vorsichtig mit dem Winkelschleifer eingekerbt und gebogen) in der zweiten Achse ist die Wanne ebenso das kein Gefälle zu dem Kühlmittelablauf besteht. Dies ist zwar etwas nachteilig aber mit meinen Fertigungsmethoden nicht anders zu bewerkstelligen. Die Stirnseiten sind dann in die Wanne eingeschweißt. Das Einschweißen der Stirnbleche habe ich mit 1,5mm Elektroden, 35-40 A und in PG (Fallnaht) vorsichtig umgesetzt. Die Wanne musste ja wasserdicht werden. Die Wanne selbst habe ich dann in den unteren Rahmen ein und aufgeschweißt.
Verkleidung_2 (Steffel)
Verkleidung_3 (Steffel)
Verkleidung_4 (Steffel)
Vor dem Lackieren habe ich Übergänge von Blech auf Kastenprofil sprich die innenliegenden Ecken und die Ecken der Wanne und deren Übergänge zum Rahmen mit Karosseriedicht ausgefugt/abgedichtet und dann überlackiert. Damit ist alles extra abgedichtet und sieht auch gefälliger aus durch den Fugenradius.
Die Scharniere der Tür und der Verschluss sind beides von der Fa. Ganter, vorteilhaft ist hier das man als Privatperson beziehen kann und es die 3D Modelle der Komponenten gibt.
Die 45° Gärungen der einzelnen Rahmenteile habe ich im Vorfeld gesägt und mit der großen Fräse exakt auf Länge gebracht da mir eine entsprechende Säge fehlt.
Bei der Suche nach einer geeigneten Arbeitsraumbeleuchtung habe ich lange nach Lampen mit Schutzgrad IP65 oder besser gesucht. Erst wollte ich eine Lampe mit 24V was aber preislich sehr intensiv war bzw. nicht in den Formen gab wie ich sie gern haben wollte. Ich bin dann doch auf 230V umgeschwenkt und habe dann eine erschwingliche Lampe gefunden. Nun war die Frage wie diese sinnvoll befestigen.
Hier hat mir ein Bild aus dem Internet von einer CNC Fräse aus der Industrie die entscheidende Anregung gegeben. Ich konstruierte aus Kastenprofil 80x50x3 einen Kabelkanal in Form eines L, welcher fest mit dem unteren Rahmen verbunden ist. Das ende mündet in einem Wasserdichten Stahlblechkasten welcher als E-Kasten mit Frontblende für Steuerfunktion dienen sollte. Bis dahin war der E-Kasten mit Bedienelementen an sich nicht geplant. Erst durch die Suche nach einer Lampenaufhängung ergab sich dieser Sachverhalt. In dem E-Kasten oben habe ich letztendlich alle Funktionen eines CNC Handrades integriert und den Not-Halttaster sowie die Drehzahlanzeige welche von der originalen Maschine stammt.
Gleichzeitig war auch geklärt wie ich mein Kabel an den Schrittmotor der X-Achse bringe durch eine hängende Schlaufe im Kabelschutzrohr aus Metall. Dadurch entfiel eine Energiekette oder gar eine lose Kabelschlaufe in der Spänewanne. Letzteres wollte ich unbedingt vermeiden.
Zusätzlich zur Lampenunterbringung war auch der obere Rahmenteil durch das fest eingeschweißte Kastenprofil gut versteift.
Verkleidung_6 (Steffel)
Verkleidung_5 (Steffel)
Frontplatte_1 (Steffel)
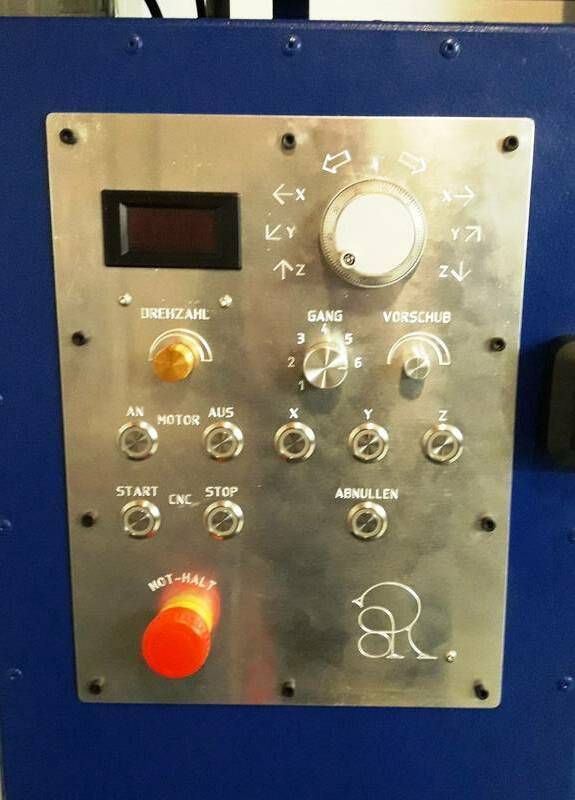